3D Concrete Printing in Action
AKO UK are supplying their VMP plastic Pinch Valve in DN25 (product code VMP025-03XK-72) into a concrete slurry application, which is used as a fail safe option. The concrete slurry with very fine aggregates in size 0.3-1mm is used for robotic concrete printing.
The world’s first commercial 3D concrete printing robot is currently in design production, with the aim to be used on site to produce a variety of elements including cladding panels. The first commercial machine is hoped to be ready in approx 14 months. A prototype has been worked on over the past 2 years.
Towering above the average person, the advanced six-axis robot is fitted with a computer-controlled printer nozzle, attached to a gantry and a robotic arm, which deposits a high-performance concrete. Approx 10mm in diameter of concrete is extruded from a nozzle in the shape of a bead, which rapidly makes passes back and forth, laying down large amounts of concrete until an entire 3D object is created.
More information on the robotic printing arm machine can be seen with the technology in action.
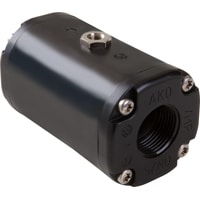
Compact plastic Pinch Valve: VMP025-03X-K72
Pinch Valve Application Details
- Media: Concrete slurry, aggregate size 0.3.1mm
- Process temperature: Ambient
- The Pinch Valve is normally closed.
When using the previous equipment that utilised a pneumatic cylinder, the company found that there were safety considerations to resolve. When the system over pressurised, there was no safe way to release the pressure as it would jam the cylinder actuation.
The company looked at different outlet types and decided on a pinch valve as the most suitable option. The pneumatics can be disabled to release the integral pressure of the system. Also any over-pressure will force its way out of the pinch valve so the internal pressure never rises to dangerous levels.
The pinch valve was also lighter than the previous system and the company managed to significantly reduce the system weight (the original system was 40kg+, whereas the DN25 VMP Pinch Valve weighs just 0.5kg.
The research engineer of the manufacturing technology company said:
“We are pretty satisfied with the Pinch Valve, and are particularly impressed by the AKO range. It’s good to know that the process can be scalable in the future if we need larger valves.”