Aerators are small rubber components which, when fitted to hoppers, silos or bins, give off a vibrating movement when air is applied to them, causing any bridged, rat-holed or trapped media stuck inside the vessel to shake itself free and drop back down into the product flow.
Although aerators are small, they play a big part in the transport of products being discharged through hoppers and silos. The effortless and free flow rate of media such as grains, cohesive powders, pellets, sludge, feed etc inside these vessels is important for efficient operation times. Therefore, aerators installed within these applications are highly useful pieces of equipment.
Is your product discharging correctly?
Rat-holing causes a funnel flow effect, thus creating a poor flow of material. Scraping and cleaning out hoppers, silos or bins is an unwanted task and causes manufacturers to intervene. By using a mallet to hit force on the outside of a vessel, or by using a rod to scrape the inside can cause damage to the equipment or the product and will ultimately slow down production.
Bridging in silos and hoppers is a result of friction on the inner walls slowing the rate of flow and restricting the material from moving freely. Particles then bind together to form an arch above the outlet area. This either severely limits the flow or stops it completely.
Caking creates resistance to flow in bins, hoppers and silos and can result in a build-up of residue on walls and the surfaces of equipment. The most common cause of caking is moisture migration due to temperature changes with materials that are soluble.
Solve Bridging, Caking & Rat-Holing Problems in Silos, Hoppers & Bins
With the use of vibrating aerator pads installed onto silos, hoppers and bins, all of the above issues can be prevented and will save downtime. Aerators also prevent material becoming wasted.
AKO have put together some case studies from some of our customers who have kindly provided information about their experience using aerator pads.
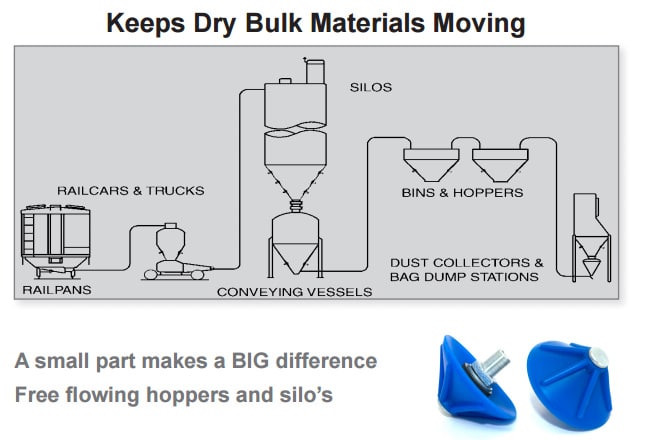
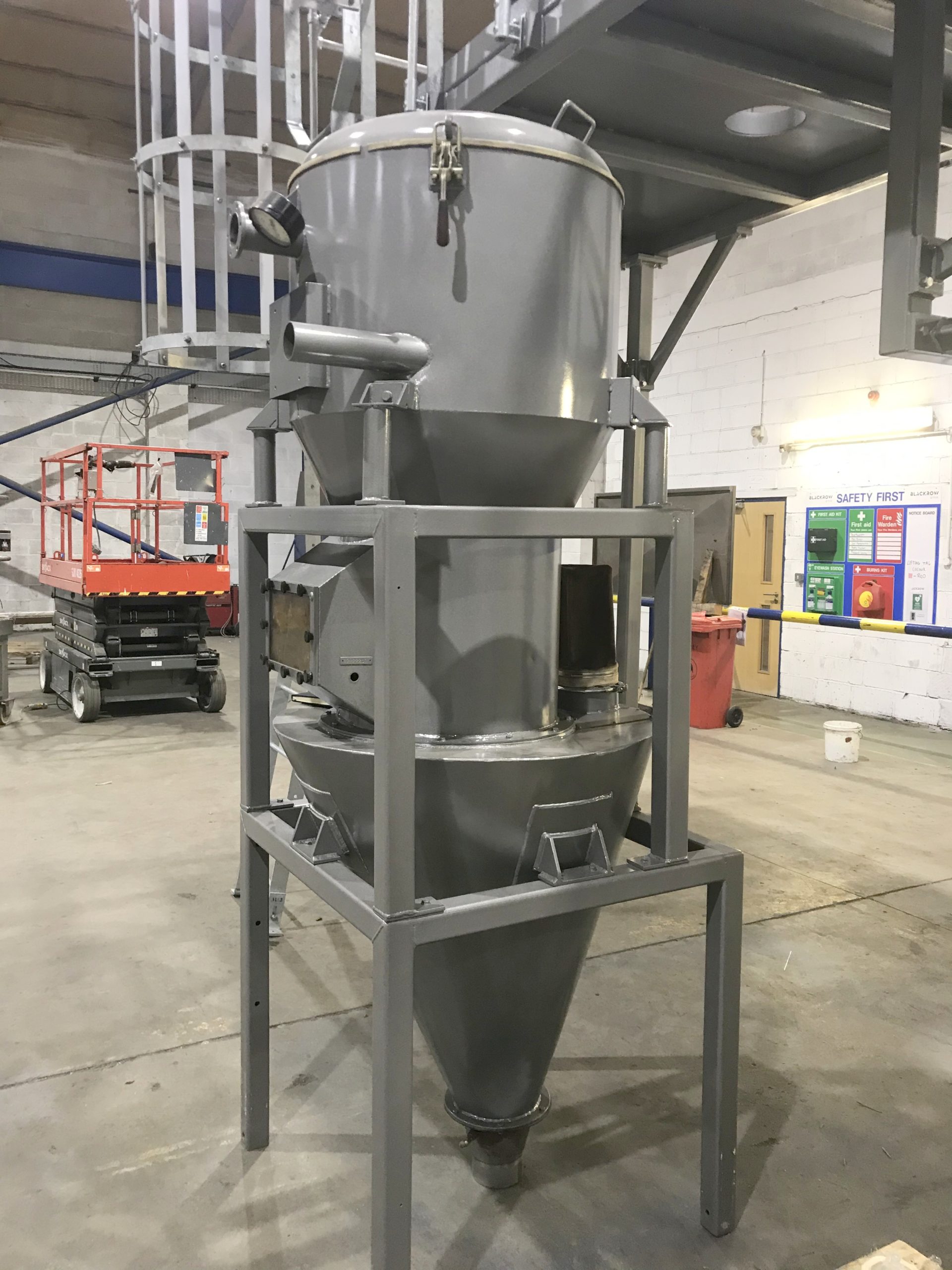
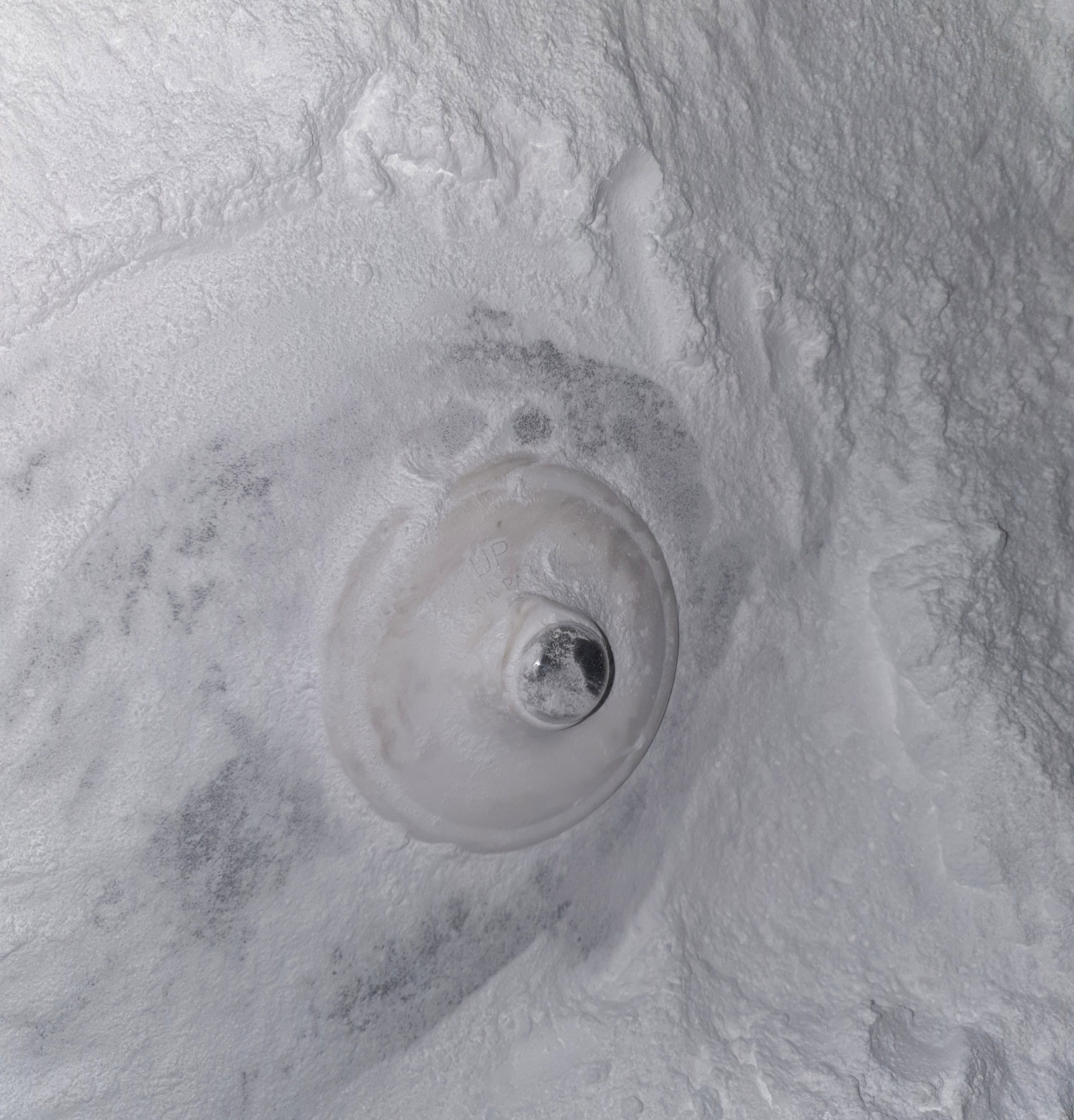