Users in the foundry industry know that to get the most out of their state-of-the-art moulding lines, the moulding sand has to consistently meet very stringent quality criteria. AKO Pinch Valves are top quality, reliable flow control solutions for foundry users, and provide lightening fast automatic shut off times for efficient operation. This means that the moulding sand is handled in the best possible way, with AKO’s abrasion resistant rubber sleeves inside the Pinch Valves.
Pinch Valves in Potentially Explosive Atmosphere
This particular site required the Pinch Valves to be ATEX rated Zone 20 inside and Zone 22 outside. This means that potentially explosive dust/air clouds will not occur under normal conditions. However, they can occur very rarely for a limited amount of time in exceptional cases. Therefore, EX Conformed Pinch Valves were supplied with conductive sleeves.
Usually, if a Pinch Valve is going to be installed in an ATEX rated Zone 20 area, AKO would supply stainless steel valves from the VMC range only. However, because this application only required Zone 20 on the inside, then AKO’s aluminium bodied Pinch Valve from the VF range was suitable to supply to cover Zone 22 on the outside, and the end user was happy with the choice.
The media passing through the pipelines and Pinch Valves are coal dust, silica sand and bentonite. Although coal dust is the only ATEX product, the project engineer decided to standardise all of the Pinch Valves so that the users on site do not mix them up and put a non-ATEX valve onto the coal dust line.
Below shows the Pinch Valves assembled to the pipe diverters before they were installed.
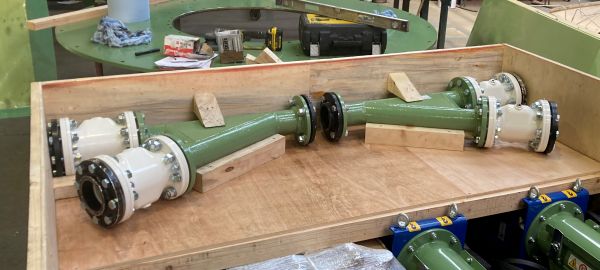
Pinch Valves used for Diverting
The preparation of the sand media within this foundry involves mixing and processing, moulding the sand under quality control, and cooling the return sand. The Pinch Valves assist with this application by controlling the diversion of coal dust, silica sand and bentonite (at ambient temperature) into various different hoppers in a dense pressure conveying system.
The maximum pressure of the above media is 4 bar. The Pinch Valves for coal dust, silica sand and bentonite are installed horizonally in the pipeline, with one valve normally open and one valve normally closed. The valves perform approximately 4 cycles per hour, sometimes more.
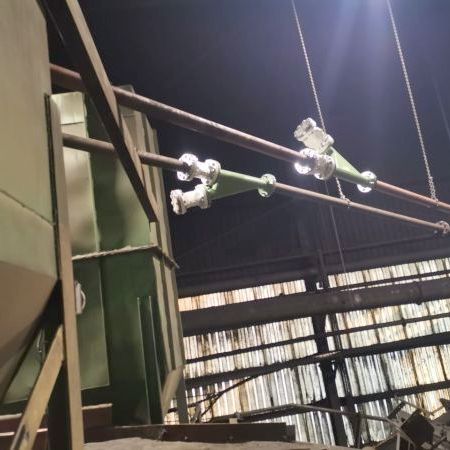
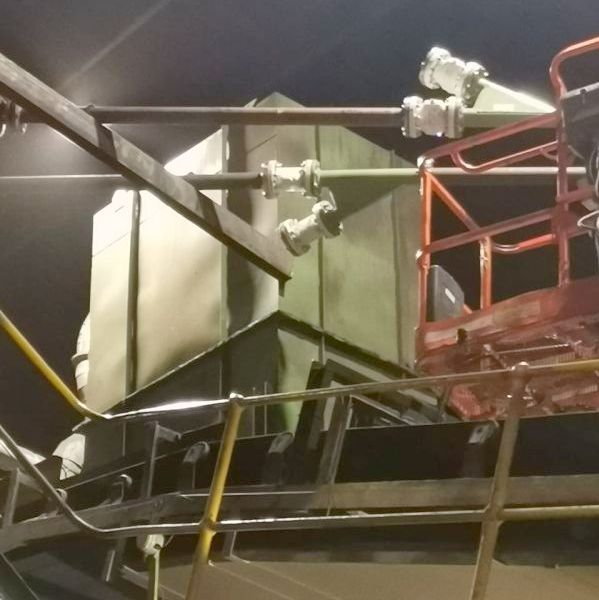
Pinch Valves have an Excellent TCO
The company supplying AKO Pinch Valves to this site via AKO UK work with turnkey solutions, project engineering and management for the bulk solids, raw materials, handling and processing industries. They have installed AKO Pinch Valves on many pieces of machinery all over the world over many years, with the project engineer stating that AKO valves are the right product for their applications.
Pinch Valves used within this application: VFX080-03LF-31-30LA
VF model, air operated, aluminium body, aluminium flanges PN10/16 with mild steel bushings, natural rubber conductive sleeve. Conformed to EX Zone 1/21 & 2/22.
Their overall satisfaction with the AKO Pinch Valve is good, with no problems. Pressure switches also accompany the valves on this site, for the user to determine if the valve is open or closed.
Spares and replacements are provided on this site, although the Sleeve inside a Pinch Valve is the only wearable part, giving the complete unit an excellent total cost of ownership.
Advantages with Abrasion Resistant Pinch Valves
Silica sand, also known as quartz sand, white sand, or industrial sand, is made up of two main elements: silica and oxygen. It is the primary component in a variety of building and construction products. Although it’s particles are slightly finer than regular sand, it can still be an abrasive media but AKO Pinch Valves handle sand well, if the correct operating procedures are followed.
Pinch valves comprise of a superior-quality elastomer sleeve in their housing, which is up to 3 times more robust and resistant to wear from abrasion than an all-metal valve. Moreover, it is the only part that comes in contact with the sand flowing through the valve, and hence is the only replaceable part. There are no dead spaces or crevices in a Pinch Valve which can result in the entrapment of material. Also, the high flexibility of the elastomer sleeve inside the housing enables close drop-tight, ensuring little to no loss of material.
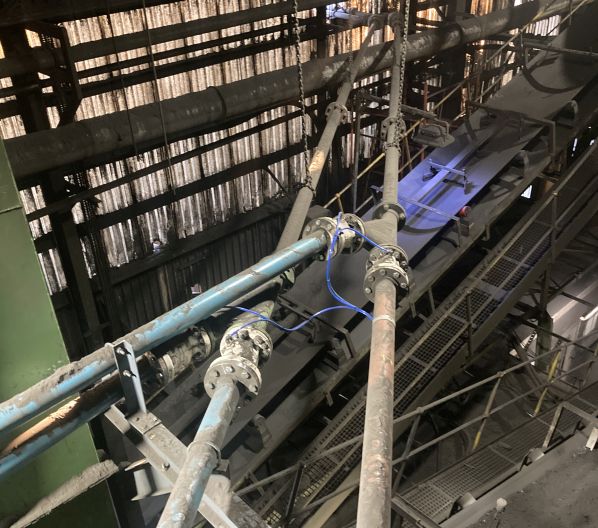