A food and beverage company are using a quantity of four VMC type DN50 Pinch Valves on their compacted coffee plant, with two hot spares used in rotation. The company were originally having to replace the valves on the plant every 4 weeks, as they were starting to wear through, and the outer of the sleeve was starting to show.
AKO Pinch Valves can be resistant to wear if using the correct type of rubber sleeve for the application, under the correct operating guidelines.
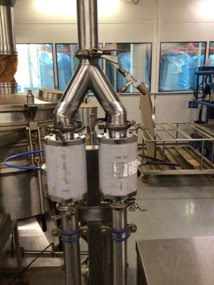
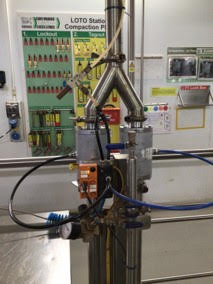
AKO UK were able to provide this end user with some helpful advice and information to prevent such early failures.
Valves for Coffee Granules: The Application
There is no additional heat added to the compacted coffee granules, so they are running at room temperature. The pressure in the lines is under vacuum to pull the coffee through, and the air pressure used to close the valves is regulated at 3 BAR. The valves for coffee granules (controlled on an ASI solenoid block) are normally open (air off), and one valve goes through around 325 cycles per hour, with the second valve completing around 160 cycles.
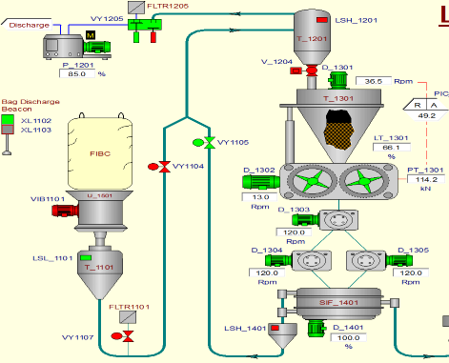
The pinch valves for coffee granules are labeled VY1104 and VY1105, they work in opposite to each other, so one can only be open at once. However, they both can be shut at the same time.
Pinch Valve used within this application: VMC50.02X.50T.30LX
VMC model, air operated, aluminium body, stainless steel tri-clamp ends, FDA Approved white food quality natural rubber sleeve.
The Solution to user error
The problem with the operating of the Pinch Valve is that the vacuum pressure of pulling the coffee through was above 300 MilliBar, causing the sleeve to pull partly closed from the inside, thus causing restriction of flow and also an obstruction where the coffee granules were hitting when being pulled through. This in turn was causing early wear of the Pinch Valve Sleeve.
The objective is to keep the Pinch Valve 100% open so that less wear is caused, and the media can flow through a full bore freely.
- Solution #1: When the vacuum is active and the coffee granules are being pulled through, then the same vacuum should be piped to the inlet of the Pinch Valve to equalise the pressure, therefore keeping the Valve 100% open.
- Solution #2: Installing an AKO.VAC system, which effectively pulls the sleeve open if required, or prevents the sleeve from closing under vacuum.
- Solution #3: Change the Sleeve quality from Natural Rubber FDA Food Quality Sleeve (M050.02X) to an EPDM Black FDA Food Quality Sleeve (M050.04HTEC).
Results after operating advice
The food and beverage company decided to pipe the same vacuum pressure into the inlet of the Pinch Valve for coffee granules to equalise the pressure, and have also switched to an EPDM food quality sleeve. This has given them much longer service lifetimes, allowing production to continue without interruptions.
AKO keep many sleeve sizes and varieties in stock, available for next day delivery, but advise for spare sleeves to be kept on the shelf, just in case of emergency failures.