A UK-based cast iron foundry working closely with their customers in the oil and gas, industrial, engineering, and architectural sectors to tailor their services to their specific needs are using valves within their mould casting process. They specialize in manufacturing high-quality products from cast iron, SG, and Ni-Resist metals.
Importance of Valves for Iron Foundry
Dedicated to manufacturing components with the highest level of integrity, ensuring that their customers receive the best possible products and services, the casting company need the best possible equipment within their foundry to achieve this.
That’s why they have been using AKO Pinch Valves in their iron foundry for over 40 years.
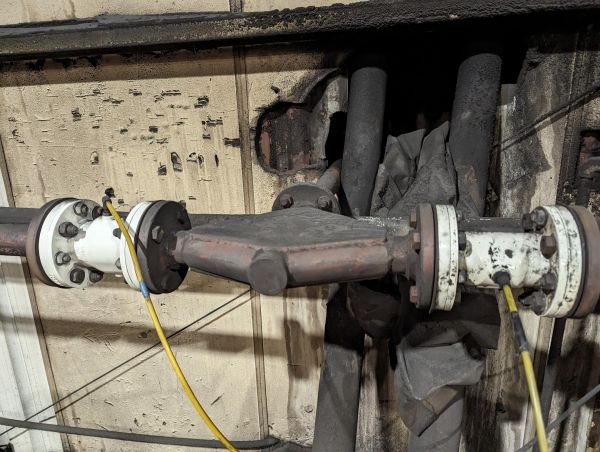
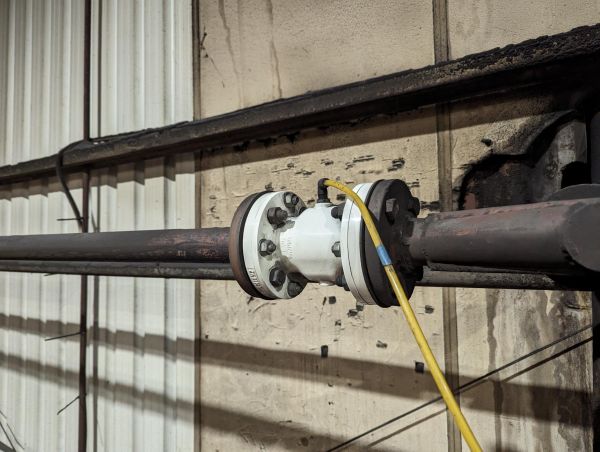

Silica sand is passing through the valves at an ambient temperature of around 16-30 degrees C, and at a pressure of 5 to 6 bar. Installed either side of the pipe tee, the valves switch to open and closed on and off. 8 bar is used to fully shut off the valves with compressed air. The valves are very important components to the directional pipework in this foundry. Without them, the flow of silica sand would not be controlled.
Pinch Valves Provide Excellent TCO
The valves are used for directional filling of different hoppers. The iron foundry decided to use Pinch Valves for this application as they believe they are the best valves for the job. The foundry are very satisfied with the overall performance of AKO Pinch Valves, in particular because the rubber sleeve inside the valves lasts up to 5 years before they need replacing. With the anti-abrasive sleeve being the only replacement part, the Pinch Valve is not only reliable but also has an excellent total cost of ownership (TCO).
Pinch Valve used within this application: VF050.03X.31.30LA
VF model, air operated, aluminium body, aluminium PN10/16 flanges with mild steel bushings, natural rubber sleeve.
The part number for the replacement sleeve inside this Pinch Valve is M050-03X. No fitting kit is required to replace a sleeve at this size, but AKO lubricant paste is recommended. For larger bore sizes from 100mm upwards, a fitting kit is recommended.
To replace the sleeve, the end connections are removed (in this case, flanges) by unbolting them, the sleeve is pulled out, and a replacement sleeve is pushed back in with the aid of some mounting paste. Full assembly instructions are available for all AKO valves, as well as technical videos which show the step by step process.