A glass bottle manufacturing company using VF type Pinch Valves are using new design techniques and new ways to recycle and save energy.
Pinch Valve used within this application – VF100.03X.31.30LA
VF model, air operated, aluminium body, aluminium flanges PN10/16 with mild steel bushing contact parts, natural rubber sleeve.
The company produces distinctive and innovative glass packaging in all shapes and sizes for the world’s biggest brands and offers a choice of almost 20 different colours.
Being infinitely recyclable, a glass bottle or jar can be made into a new one over and over again, with no loss in quality or purity. Making new glass bottles and jars from recycled glass reduces the amount of energy needed in the production process and lowers emissions into the atmosphere.
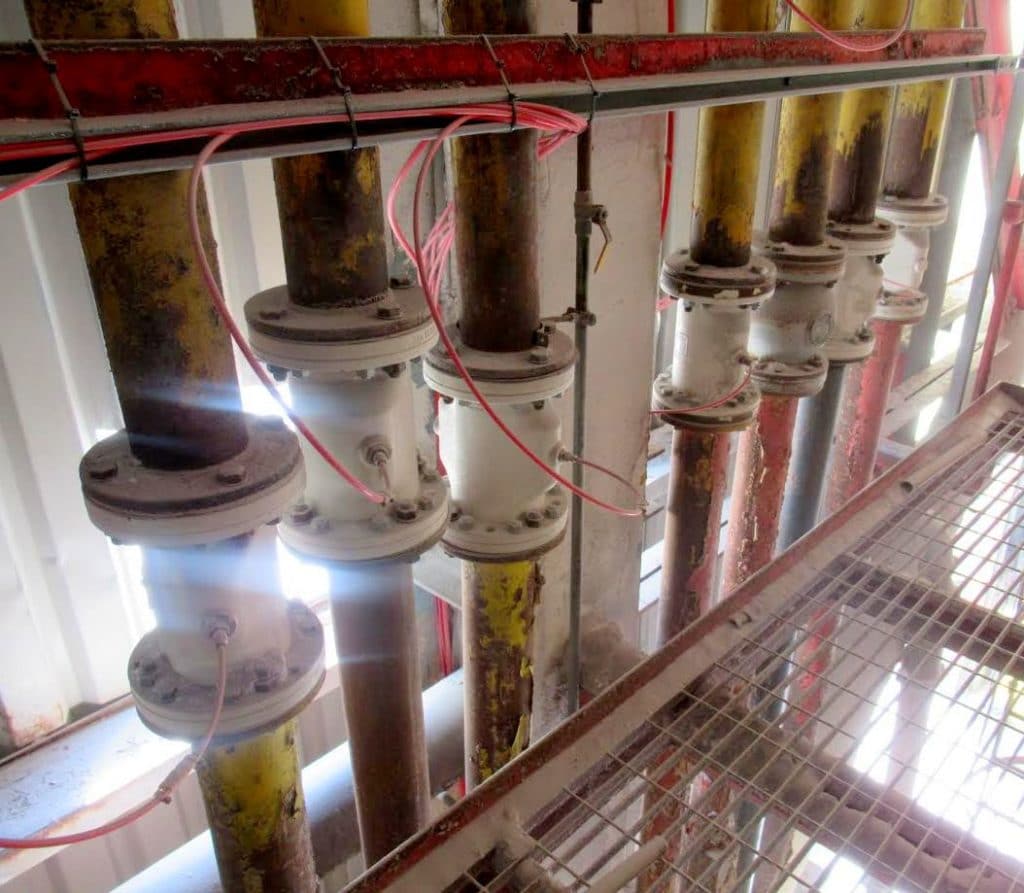
Product passing through the valves:
- Soda ash
- Limestone
- Spanish Dolomite
- Sodium Solphate
- Nephelyne Syenite
- Calumite
Temperature: Ambient
Line Pressure: Between 1 – 1.5 BAR
Control Pressure: 30 PSI
The valves are normally closed to prevent material contamination.
Amount of cycles per day: Across all the materials, on average 30 deliveries per week.
No degree of vacuum is being used.
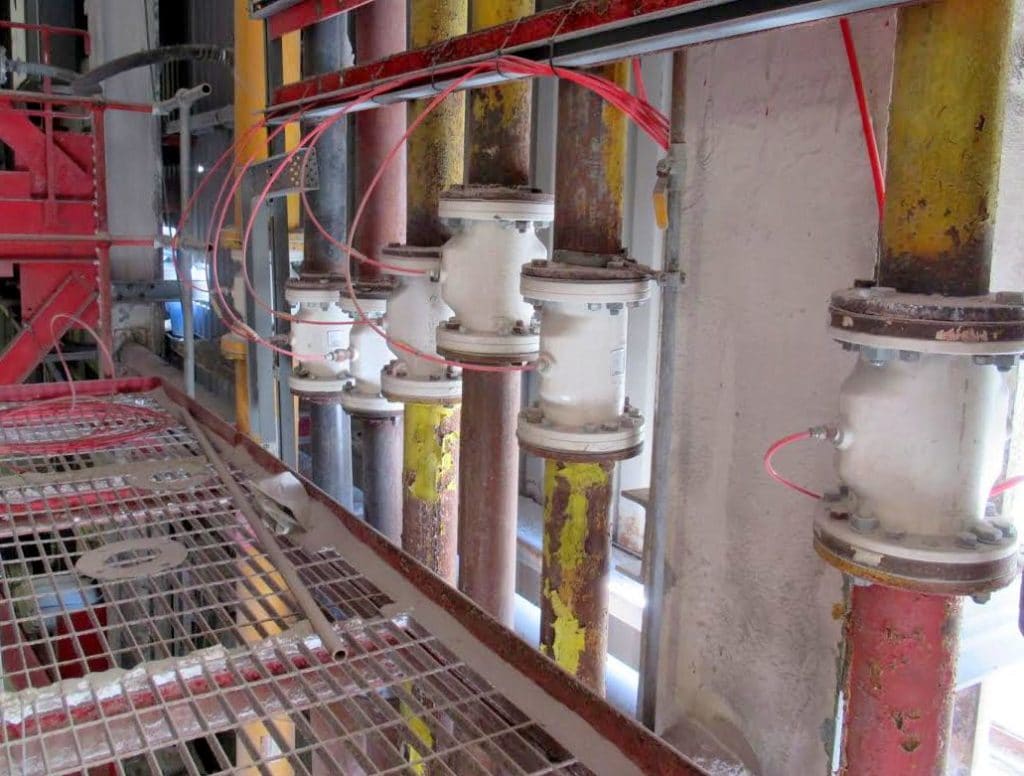
The glass container manufacturing company have been using Pinch Valves since 1991. Pinch Valves are replaced on site approximately every 6-12 months.
The Plant Maintenance manager on site said:
“Our overall satisfaction with AKO Pinch Valves is very good. We expect our increased failure rate is due to larger grain sizes being supplied to us.”