A pharmaceutical and chemical processing company are using Pinch Valves from AKO UK’s VMC hygeinic range on transfer lines between upstream client drums and a vacuum tray dryer.
Application Details
The product is exotic methylosiloxane OS-20 mixed with some kind of Resin beads. The valves are isolating the mixing tank and then opening it up to a lobe pump that pumps the mixture out of the mixing tank to a tray dryer. The mixture is at ambient temperature (up to 40°C) at this point. Outside the tray dryer there is a 0.5’’ distribution manifold that is divided between 6 trays. Each of the manifolds branches has the pinch valve fixed to it and it opens while the pump meters in a certain amount of the mixture to the tray. The valve then closes, and another valve opens and the sequence is repeated until all the trays have their fill.
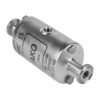
Pinch Valves used within this application: VMC15.05K.50TA.50 & VMC50.05.50TA.50
VMC model, air operated, stainless steel body, stainless steel tri-clamp ends, viton sleeve.
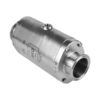
The product is then heated up to 200°C, however the valves are located outside the tray dryer which is isolated so the temperature does not reach the valve. The pressure is 1 to 2 barg max from the pump.
The pinch valves are normally closed with a full vacuum of 0.43 absolute applied, and open a couple of times per batch. The machine operates one batch per week, but not every week.
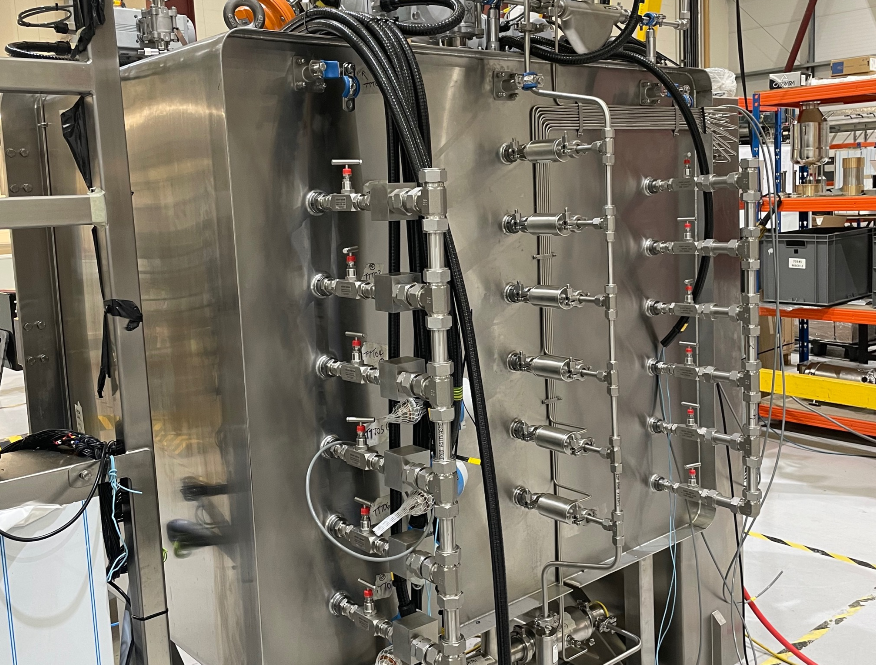
Reasons for Selecting Pinch Valves
The Client specifically requested pinch valves to have capibility of replacing the seals as the resin beads have a tendancy to stay on the seals.
Furthermore, the pharmaceutical company favoured the clean design of the Pinch Valve. The company’s process engineer chose a Pinch Valve for the design of this machinery during the research and development phase, and explained that Pinch Valves assist with the application with no retention as on other valves such as ball valves & diaphragm valves. He also liked the fact that Pinch Valves are easy to clean through.
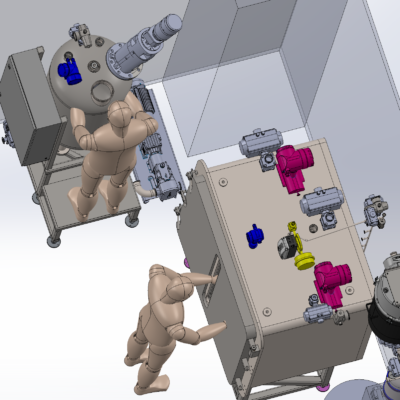
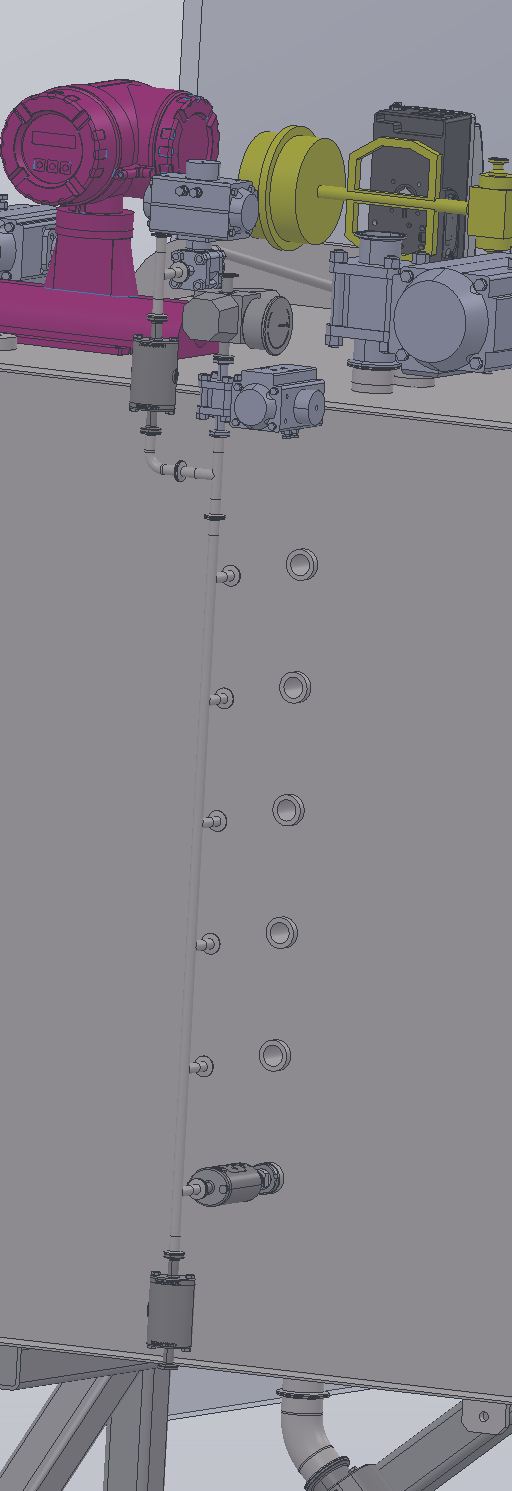