AKO UK supply pinch valves to a powder coating company situated within a fairly small premises. They powder coat metal parts such as beams for shops including Topshop and BHS. The company also have a contract for powder coating the railings for the London Underground.
The company started using AKO pinch valves from the VM product range when they purchased a machine from an Original Equipment Manufacturer nine years ago, where the valve for blast washing was already installed. The machine is like a huge dish washer. The parts that are due to be painted (powder coated) are blast washed inside the machine initially. Once the washing process has finished, the door opens and the pinch valve opens, allowing the water to empty from the machine.
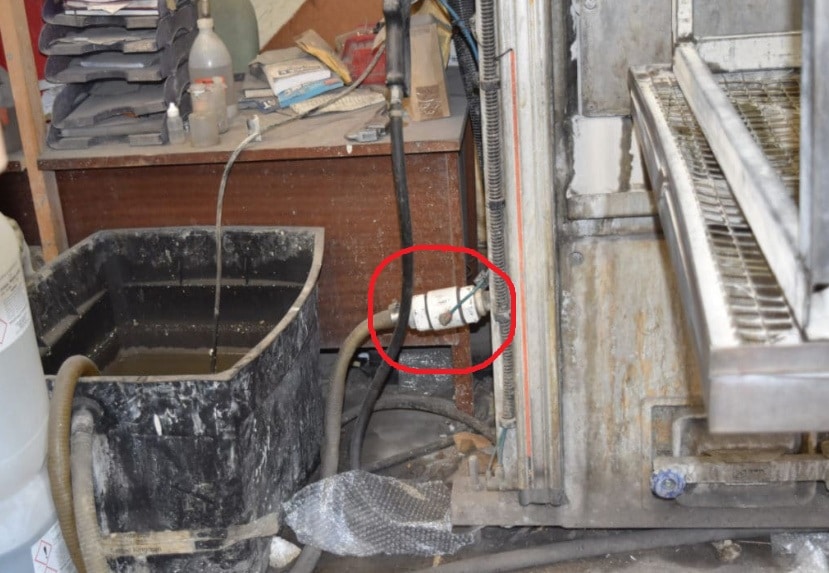
Mixed with the water to wash the parts is 3% of iron phosphate cleaner at 67 degrees C. The cleaning mixture is gravity fed through the valve, which is position at the side of the machine low to the ground. The pinch valve for blast washing is normally open when not in use. The valve is in the closed position when the machine is filled with water and the washing process is in progress, which then opens again to drain the product. The air pressure being used to close the pinch valve for blast washing is 2.5 BAR, and 30 cycles per day are carried out on this site.
Pinch Valve used within this application: VM020.03X.70.30LA
VM model, air operated, aluminium body, POM plastic BSP threaded end connections, natural rubber sleeve.
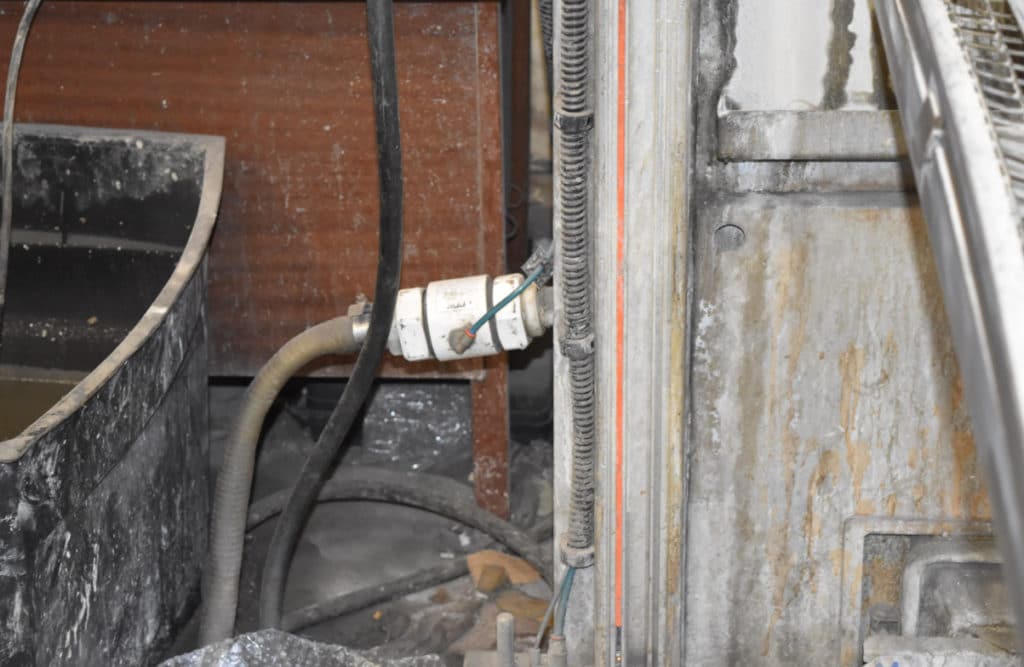
The powder coating & blast washing company re-sleeve the pinch valve on the machine approx every 18 months. They order 2 sleeves at a time (sleeve product code M020.03X) so that they can keep one on the shelf as a spare for emergencies.
Darren, one of the workers at the premises is satisfied overall with the pinch valve for blast washing and powder coating and has no concerns regarding the performance of the product.