A company producing MFC (microfibrillated cellulose) with a mineral content ranging from 0-80% are using valves on their re-dispersal units. The material is partially dried in order to ship more economically, and is then re-dispersed on a customer site for use in their application.
Cellulose is the most adundant and renewable natural polymer on Earth. The process this company are using converts celluose, sourced from wood fibres, into its primary constituent building blocks, fibrils. These fibrils are re-engineered at micro-scale to have a large aspect ratio and high surface area, yielding an interconnecting, dense, web-like network referred to as microfibrillated cellulose. The MFC has a large surface area, allowing the formation of more hydrogen bonds within the web, giving natural strength to the material.
The MFC product is used within the following markets:
- Paper
- Packaging
- Building materials
- Agriculture
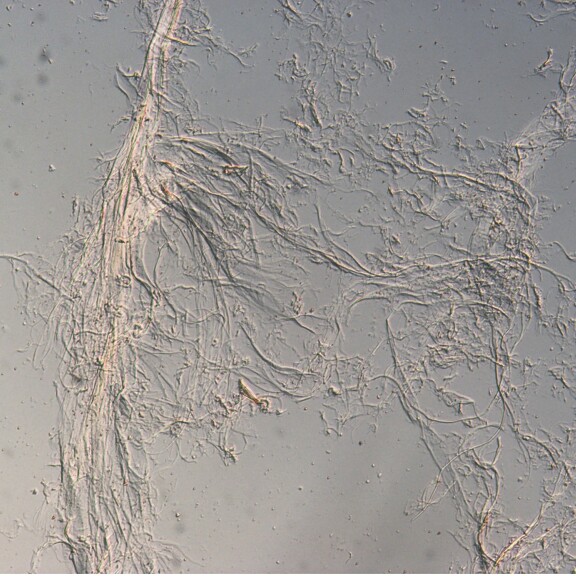
The company’s grinding process subjects fibres to gentle yet intense milling, liberating an optimal ‘microfibrillated’ network structure. MFC increases bonding, giving natural strength that allows you to reduce additives and expensive fibres or other materials.
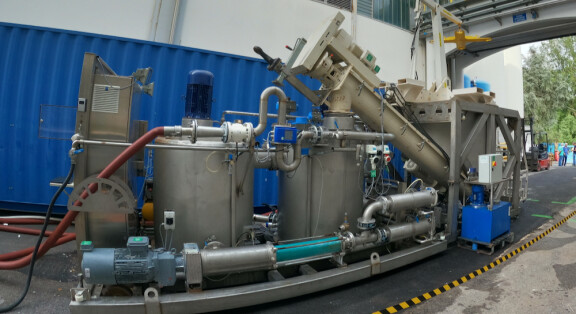
How the Valve for Cellulose Slurry assists with the application
The media passing through the valve is a co ground mineral/cellulose slurry, at 10-50 degrees C. The valve for cellulose slurry is positioned in a horizontal position, downstream of a mass flow meter. The valve is normally closed, and is at a steady state when running.
The Pinch Valve is not actually installed on a production unit. The unit is used for demonstration purposes on customer sites, the unit runs in campaigns ranging from a few hours to 2 weeks. These can occur from 3-20 times per annum depending on demand. The mobile test skids run for approx 100 hours per year.
Pinch Valve used within this application – VF080.03X.31.30LA
VF model, air operated, bore size DN80, aluminium body, aluminium flanges PN10/16 with mild steel bushings, natural rubber abrasion resistant sleeve.
In order to measure the solids content of the material within this demonstration unit, a mass flow meter is installed. This is a device that accurately measures the flow rate of a fluid moving through a pipe. It is important that any entrained air pockets are minimised in order to achieve accurate readings. The Pinch Valve for cellulose slurry is closed using approx 2 BAR air pressure, and 2.3 BAR of back pressure is applied on the slurry in order to compress the air pockets to a less significant size for the reading to be measured.
The Pinch Valves are used in conjunction with an air solenoid and regulator. The company uses pressure sensors to measure the line pressure but control is manual via the air regulator.
Pinch Valve for Cellulose Slurry Feedback
The company have been using Pinch Valves since 2013. The Engineer told us:
“The Pinch Valve provides the ability for us to control line pressure without the need for expensive valve positioners and control loops.”
The company use other types of valves, which they confirmed all have advantages and disadvantages in specific applications. For example:
“Butterfly valves are cheap and simple to replace but do not allow full flow and can bridge in certain applications.
Pinch Valves have proven to be robust, simple and reliable. They are easy to service on remote sites and require minimal maintenance. They have proven to be very well suited to our application.”
The natural rubber sleeve inside the Pinch Valve for cellulose slurry is replaced every 8 years at present. This may increase due to the increasing service cycles of the units. The company are still using Pinch Valves for this application in new units that have been built recently.