One of the UK’s leading manufacturers of high quality paving products such as block paving for driveways and slabs for patios have kindly supplied AKO UK with some information about their application. Their end products comprise of a range of garden slabs, driveway paving, porcelain paving, natural stone paving, and specialised aggregates.
Controlling Flow of Pigment Slurry with Valve
Up above this equipment in large white bags are different coloured powdered pigments. Different coloured pigments are chosen as additives, depending on the colour of batches of slabs or bricks that are being made.
An amount of the pigment is passed through a vibration unit which prevents it from sticking and clogging up around the sides. The pigment is added to water in a lower tank and is then sent to a cement mixer, where it is mixed with cement before producing the concrete slabs.
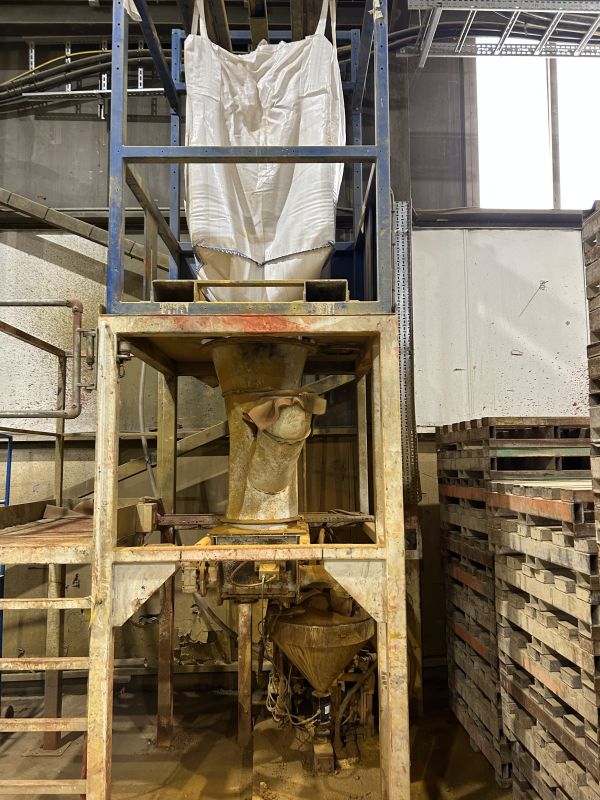
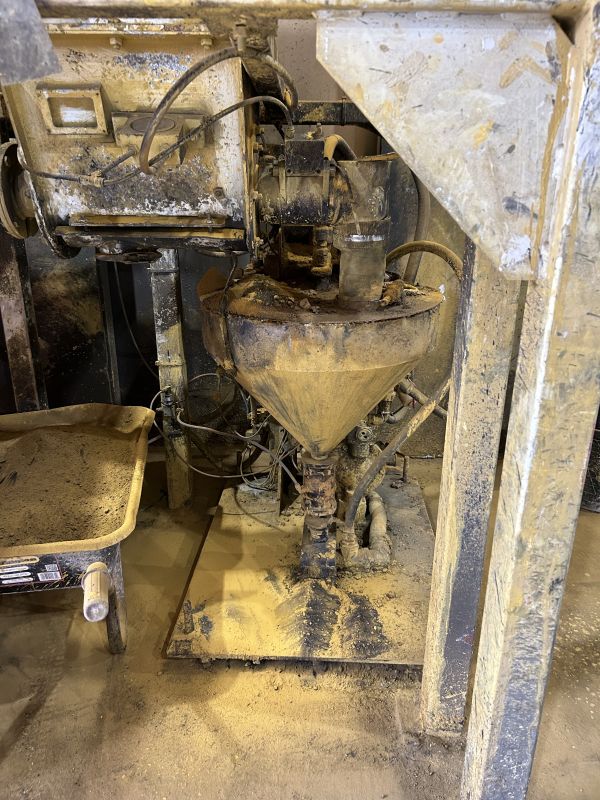

When the pigment is introduced with the concrete, it is then thoroughly mixed, and compressed into moulds to form the concrete slabs, squeezing excess water out. The concrete slabs are then transported up to a drying process.
Application Breakdown
There are a total of three DN40 black plastic Pinch Valves installed at this plant, all doing the same job but with different coloured pigment powders. The pigment powder is ambient in temperature, and is dropped down via gravity into the water tank. The slurry of mild pigment coloured water is the media that is passing through the valves.
The Pinch Valves are installed vertically at the bottom of the hoppers, and are held in the normally closed position with 2 BAR compressed air, until they are opened when required.
Each valve performs 30 cycles per hour, with the site open 20 hours per day, 4 days a week.
Pinch Valve used within this application – VMP040.03X.72
VMP model, air operated, POM body, POM BSP internal thread end connections, natural rubber sleeve.
Pinch Valve Experience
The company have been using Pinch Valves for 36 years. They were originally using a DN20 Pinch Valve from an alternative manufacturer which needed to be replaced after being damaged with a fork lift truck.
After some help from an Original Equipment Manufacturer who advised the company to increase the size of the valve for a more satisfactory performance, they swapped the original DN20 valve for a bigger bore size of DN40 Pinch Valve from AKO UK.
Since having the AKO UK Pinch Valve installed for two years to date, the company have said that they believe it is a better product compared to the previous valve, which has saved them a lot of labour time since they are not replacing the rubber sleeve as often.
The company does keep two spare rubber sleeves on the shelf in case of failures, but have not needed to replace them during the past two years.
Solenoid valves control the Pinch Valves, and pressure switches are used on an automated air system.

How was a Pinch Valve Specified?
When the original pinch valve was damaged by the fork lift truck, a floorman from a similar company manufacturing cement blocks recommended AKO UK Pinch Valves to the company, where they have not looked back and continue to successfully use AKO Pinch Valves within their pigment & cement slurry mixing process with ease.
There are four other sites in the UK for this company, of which AKO UK look forward to supplying their long lasting, reliable and cost effective Pinch Valves to improve even more workload.
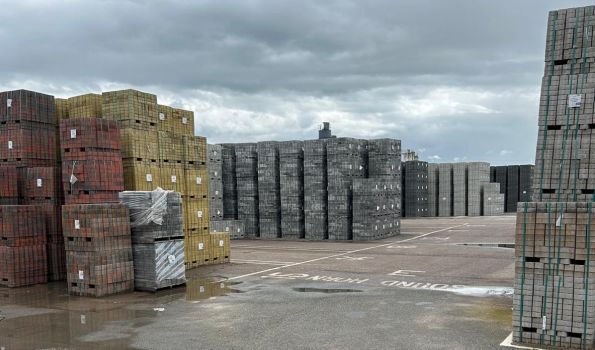