Due to demand, an original equipment manufacturer of swarf conveyors and filtration solutions for the engineering, aerospace and rail industries are supplying more and more swarf management systems into the market.
This stand-alone tank is equipped with a 10-micron duplex filter that guarantees super clean coolant is returned to the machine. This is usually delivered at high pressure via a 15 or 70 bar pump through programmable valves using “m” functions. Further improving filtration, an inline micro mag filter can extract fine grains of ferrous material.
The advanced modular tank is positioned locally to the machine, and is capable of holding large capacities of coolant. The modular tank self-monitors coolant input and output with its software to ensure it meets the machines coolant demand.
The supply of clean coolant results in; improved tool life, workpiece integrity (surface finish and accuracy) maintained, chip breaking, chip extraction, temperature at cutting point.
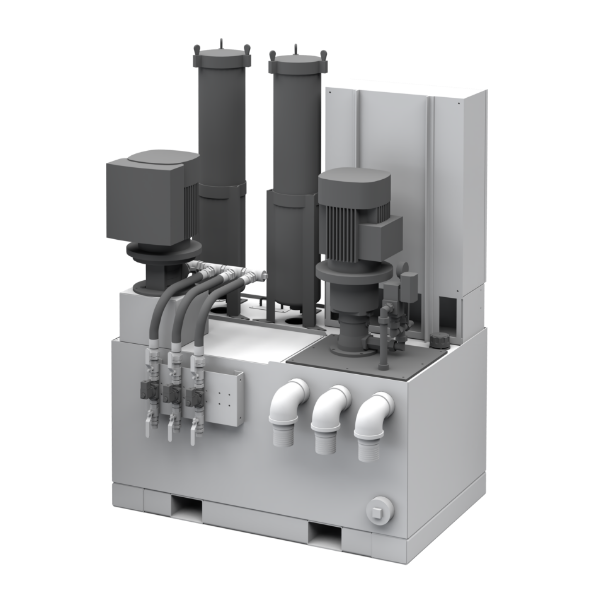
In conjunction with Hydrocyclone Filtration System
Fluid containing sludge flows from the supply pump into the filtration system via the side port and through the inlet. The fluid flows along the inner wall of the cyclone and the pressure energy is converted into rotational energy. Whilst turning under the strong centrifugal force, the heavier sludge descends the tapered body towards the narrow nozzle in the base of the system. After passing the nozzle the sludge is discharged into the sludge pod via a Pinch Valve.
Pinch Valve used within this application – VMP032.04HTEC.72
VMP model, air operated, POM body, POM BSP internal thread end connections, EPDM rubber sleeve.
The discharged sludge rapidly loses its rotational force, is collected in the sludge pod and collects until discharging, either manually or via a solenoid valve. Any ultra fine sludge which is unable to generate sufficient centrifugal force and descend down the inner wall of the separator, is discharged along with the cleaned fluid from the top port.
Pinch Valve preferred over Ball Valves
The stringy, small chipped or fine swarf is submerged in coolant and is ambient in temperature, depending on the machining environment and equipment. The Pinch Valve is normally closed using 5.5 BAR air pressure. The pressure of the swarf and coolant mixture passing through the Pinch Valve is 2.5 BAR. The number of cycles that the machine performs per day is set by the customer which is based on the machine parameters.
The OEM started using Pinch Valves within their machinery as a recommendation. They had previously used manual ball valves but find the Pinch Valve more reliable.
Ball valves tend to clog inside the cavities from a build up of dirt or sediment, making it difficult to open and close. With the self cleaning rubber elastomer sleeve which opens and closes a Pinch Valve, clogging does not happen, resulting in a 100% clear straight through bore with no dead spots. Furthermore, the Pinch Valve rubber sleeve is reinforced which makes it suitable for even the most abrasive media.
See more benefits of the Pinch Valve and how it can improve your system or equipment.
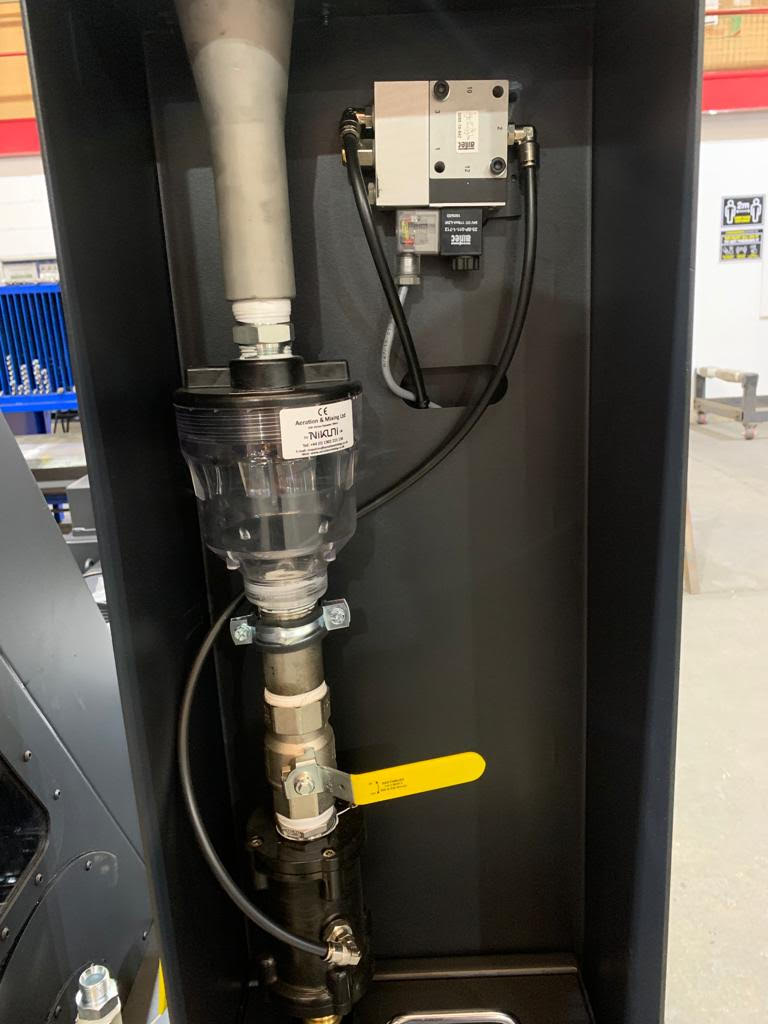