The main purpose of this company using valves for abrasive solids is to manufacture parts of drainage systems using polymer concrete (the parts underneath the drain, not the metal iron grill). The water in the application falls through this iron grill, and flows down into the part manufactured by the company, which is like a ‘U’ shaped piece of concrete.
A variety of media is passed through the extensive amount of AKO Pinch Valves on site at the company in the UK. These include aggreggates, sand, gravel, glass, calcium and carbonate. All products are ambient temperature, and flow through the valves at 4 BAR, with an air pressure of 5-6 BAR being used to close the valves. The valves for abrasive solids are all installed in various positions, both horizontally and vertically, and are kept in the open position.
Each pinch valve carries out 1-6 cycles per hour over 24 hours a day, depending on which line is running. There is no degree of vacuum being used.
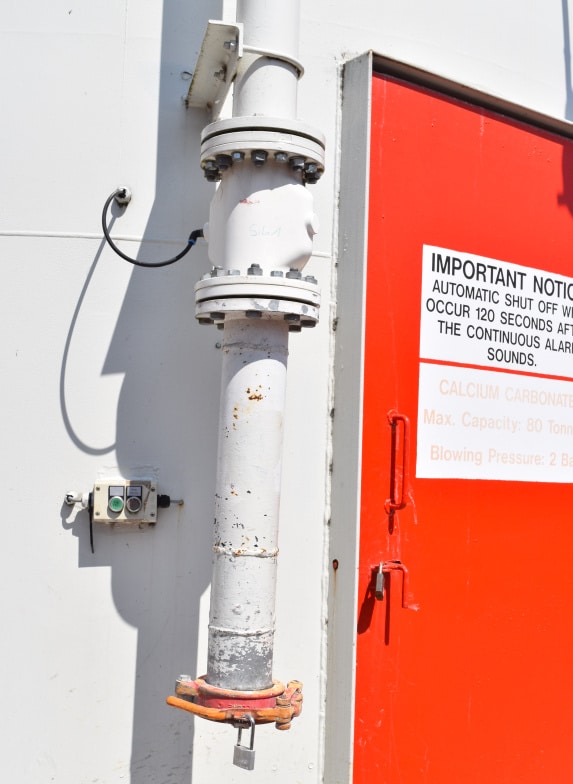
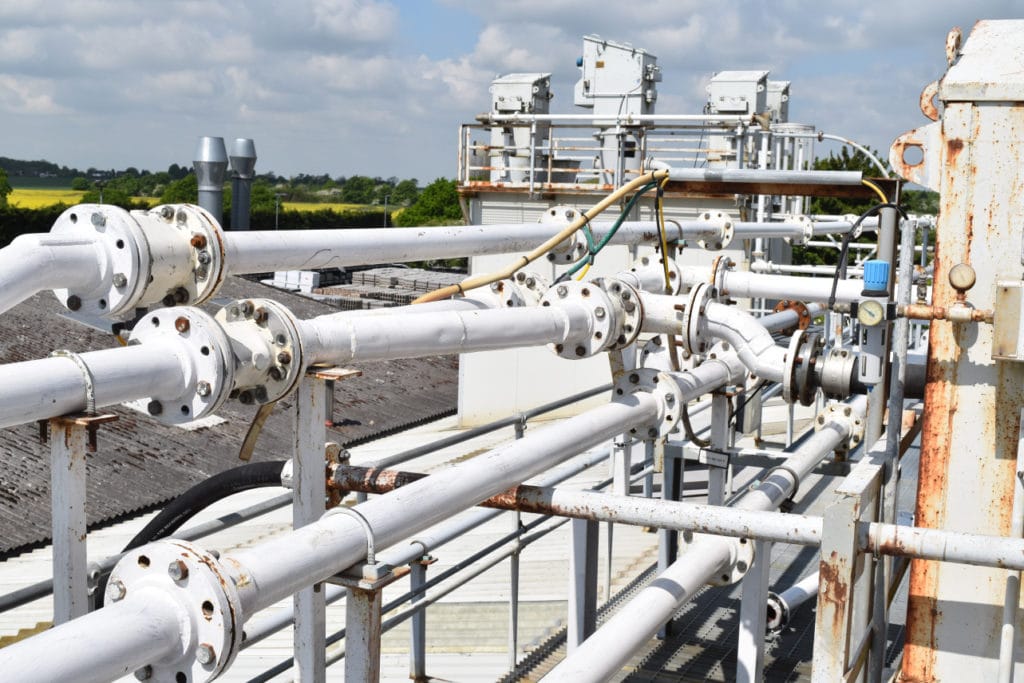
Pinch Valves used within this application – VF080.03X.31.30LA & VF100.03X.31.30LA
VF model, air operated, bore sizes DN80 & DN100, aluminium body, aluminium flanges PN10/16 with mild steel bushings, natural rubber abrasion resistant sleeve.
Depending on how often each line is used, the natural rubber sleeves inside the valves for abrasive solids are replaced every 4-6 months.
There are also accessories such as solenoid valves being used on this site.

Leon, the site manager was unaware of how the company found these valves for abrasive solids because they were already installed on the plant when he first started his employment for the company. However, the company have been using AKO products for 25+ years.
The overall plan is to continue maintaining the pinch valves that the company are using. They prefer to replace the rubber sleeves and flanges when needed, rather than purchasing brand new complete valves.
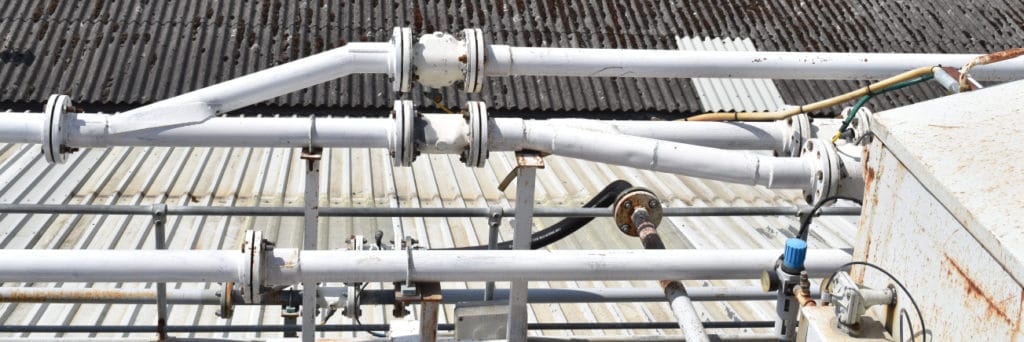