A dry pet food manufacturing site are using Pinch Valves from AKO UK in a fines re-work system to minimise waste.
Pinch Valves & Vacuum: How They Operate
There are a total of two air operated valves on site in different sizes; DN65 & DN50. The media passing through the valves is a variety of pet food ingredients in powder form, at just above ambient temperature. The valves are located next to a central vacuum pump, pulling from two separate areas.
Positive air pressure is used to operate the Pinch Valves and vacuum pump to pull product through on the other line. 3 BAR of air pressure is used to close the valves.
The valves are normally open. They go from the open position, to the closed position, and back to the open position again, every minute, running 24 hours of the day, 5 days a week.
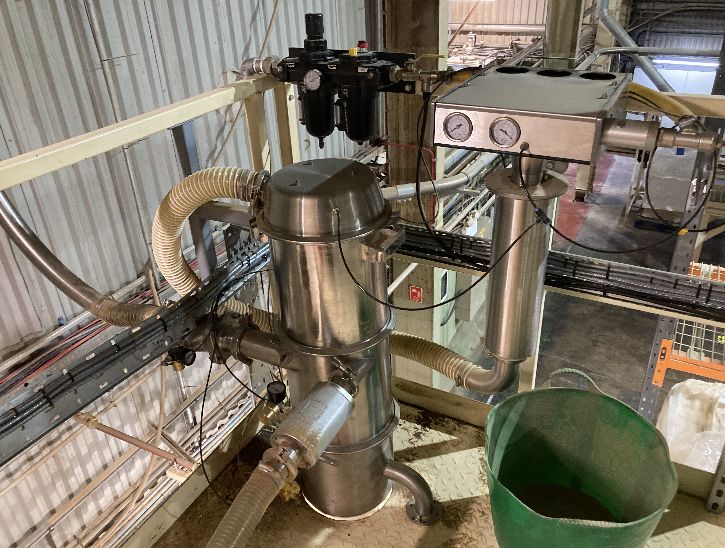
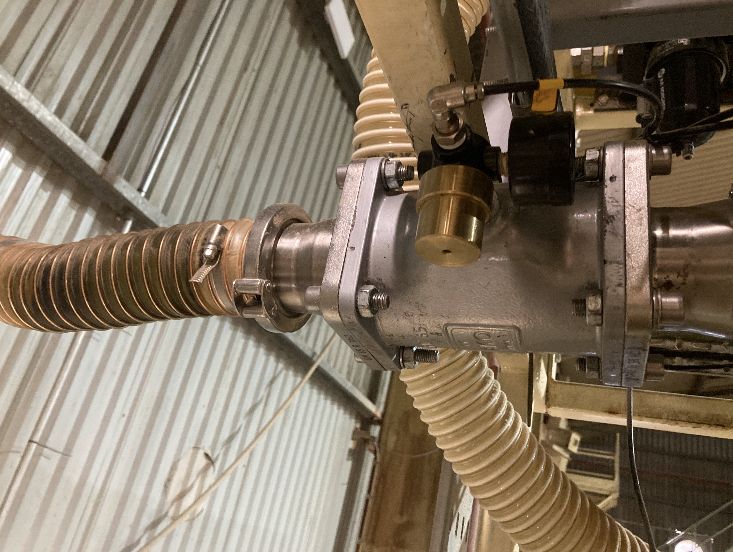
What the Application is about
The application allows dust and excess material after the extrusion and drying/cooling process to be transferred back into the system, so that it can be reused to minimise the amount of waste.
Because the site has a central vacuum unit, the company pulls from two separate lines and so the Pinch Valves are used to isolate one line, while they pull from the other (see more on using Pinch Valves with Vacuum)
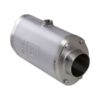
Pinch Valves used within this application – VMC50.03X.50R.30LX & VMC65.03X.50R.30LX
VMC model, air operated, Natural rubber sleeve, aluminium body, stainless steel weld-on end connections.
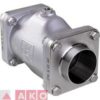
The dried pet food manufacturer have been using Pinch Valves for 5-6 years in this application. Since it was designed to pull from two different areas of the factory, the valves were part of the original designed system, as the Original Equipment Manufacturers decided that Pinch Valves would be the best solution for the application.
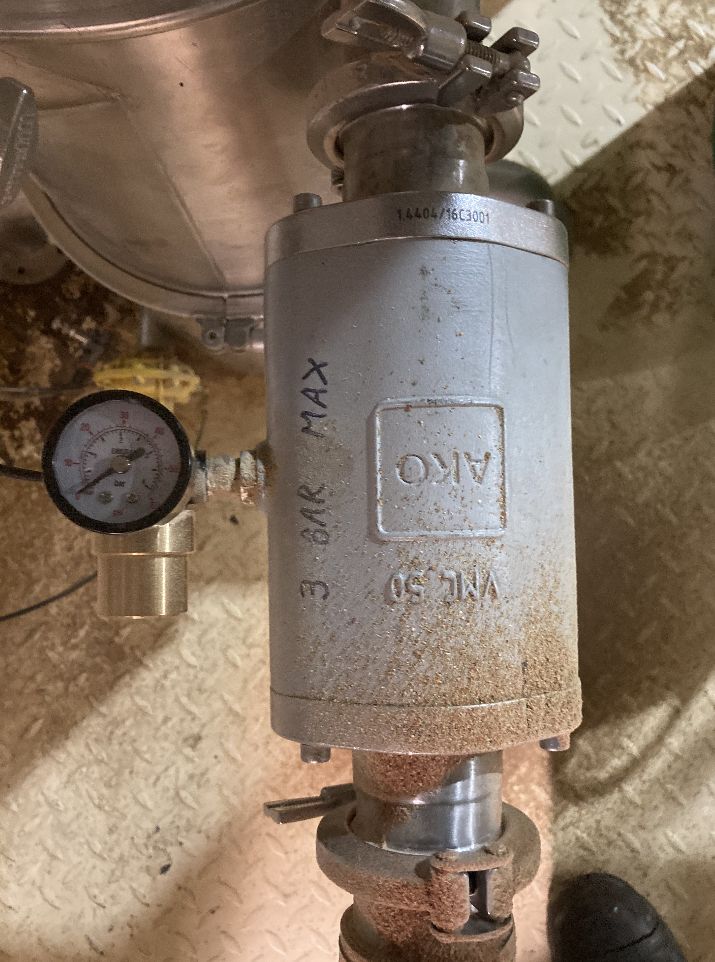
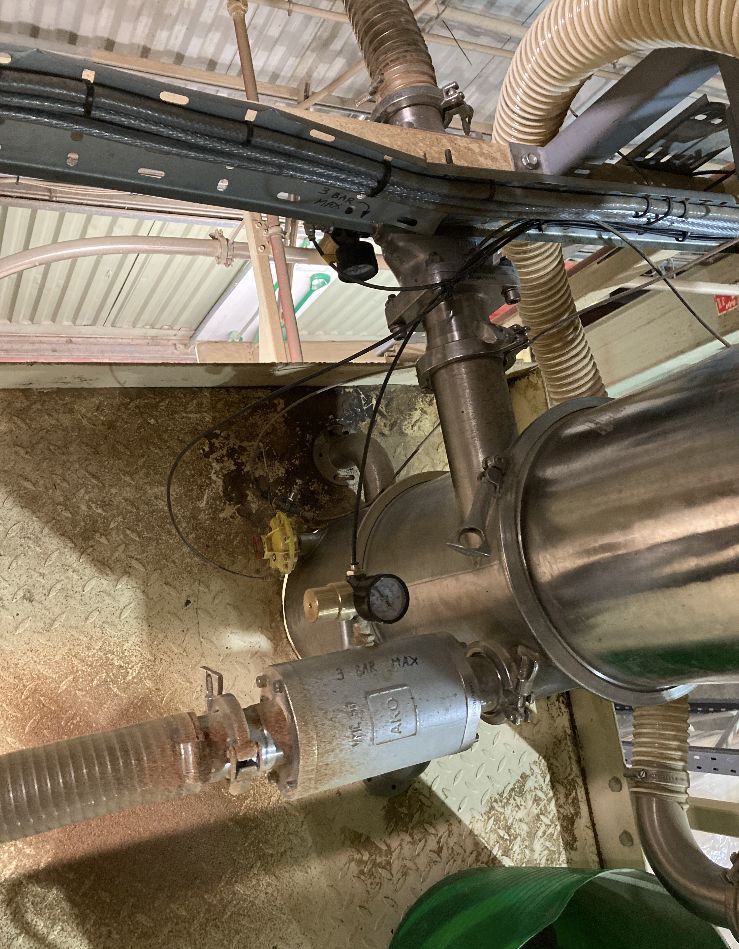
Experience with Valves for Pet Food
The pet food manufacturer found out about Pinch Valves from their supplier of Pinch Valves used in this system from the original install. They use many different types of manual and automated valves across site for lots of different processes. They have found the Pinch Valves from AKO UK to be easy enough to maintain and to work on when they have failed and require to be replaced.
The rubber sleeve is replaced approximately every 3-6 months, with spare sleeves being kept on the shelf to save downtime in case of failures. The good thing with Pinch Valves is, the sleeve is the only wearable part that needs replacing. There are no further gaskets, discs, packing, seats, plugs, stems, etc. to worry about replacing.
Fixed regulators are used to stop any changes being made to the system. Solenoids and timers are also used to switch from one side of the pull system to the other.