AKO UK are pleased to be working with manufacturers of an assortment of edible sweets including rice puffs coated with sugar and syrup. The company is based in a very old mill, which is actually now 2 mills joined together and has been like this since the end of World War 2.
To control the mass flow of these sweets, the company were originally using ball valves. However, the ball valves for sweets were becoming shredded around the seals – The seat wore away too quickly (usually within 1 month) and the existing manufacturer went out of business so they could not purchase any spares.
Jon Birch (a regular visitor to the site) was asked if he could come up with a solution to replace the failed ball valves, and had a folder full of AKO UK data sheets on his desk. When he saw the VMC range of pinch valves, these looked ideal for the application so after some communication, AKO UK supplied a sample valve to trial for 3 months. However, a degree of vacuum (260/280 mbar) was also being used so AKO UK later supplied an AKO-VAC unit for the trial. After a total of 9 months of successful trialing, the sweets manufacturer were happy to proceed with more pinch valves for sweets.
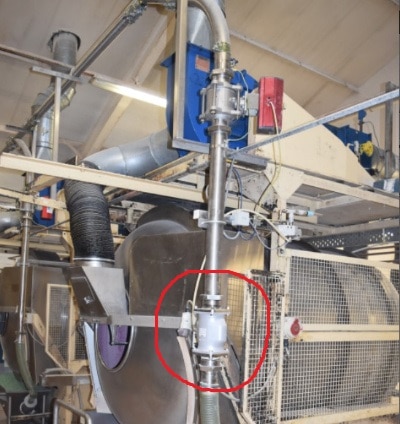
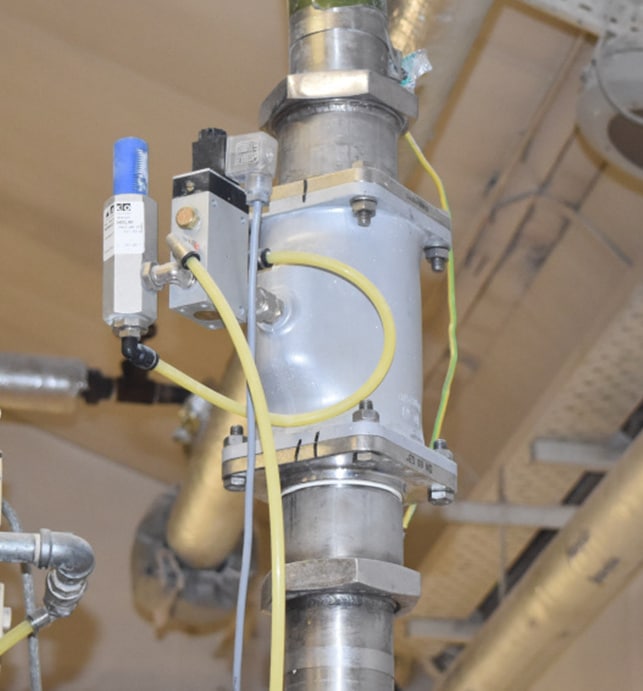
The 80mm VMC Pinch Valves used in this application are sitting vertically in line, in the normally closed position using a very minimal pressure of 30psi – just over 2 BAR. The sweets are sucked up through the pinch valve and through pipework into another room where they are then mixed with other colours in a hopper before being bagged up.
The temperature of the sweets is ambient.
Amount of cycles per day: 13-15 cycles per hour, 14-15 hours per day, 5 days a week.
To date, the sweets manufacturing company have replaced one rubber sleeve in the AKO Pinch Valve, although this was only because they were not using the vacuum system at the time and therefore the sleeve became deformed. Since the AKO-VAC system has been fitted, not one sleeve has been required for replacement.
Pinch Valve used within this application: VMC80.02X.50G.30LX
VMC model, air operated, aluminium body, stainless steel BSP threaded end connections, white food quality natural rubber sleeve.
The onsite manager is very happy with the AKO products and would recommend them to other sweets manufacturers.
There are 6 machines producing the sweets in the old mill, currently with AKO Pinch Valves on 2 of them. Once the existing ball valves fail on the other machines, the sweets manufacturing company will be replacing these with more AKO Pinch Valves and will continue to use AKO spares. Also, in the other room where the sweets are mixed, there is a 50mm pipeline with ball valves installed. Again, once the ball valves fail, the company will replace these with reliable and cost effective AKO Pinch Valves.