Powder coating is a dry finishing process that involves a spray of dry powder that is preciseley applied to an object or surface to give it a coat of paint. Powder coatings are based on polymer resin systems, combined with curatives, pigments, leveling agents, flow modifiers, and other additives.
Sand/shot blasting or compressed air blasting is the opposite effect – where a spray of sand, steel shot or air is used at a high force to remove the coat of paint, rust and other contaminations on a hard surface.
Each of these methods of blasting or coating require the use of an on/off valve to control the flow of powder or blasting agent. These are abrasive types of applications whereby the valve in situ should be abrasion resistant for a free flowing process with no breakdowns.
Pinch valves can be used in pre-treatment processes – as control valves for cleaning agents for the pre-washing stage, and in powder coating plants. Pinch valves control either the supply of cleaning agent mixed with water for cleaning or the removal of waste water. However, they can also be used within the actual coating processes themselves as control or dosing valves for the transport of powder coatings or for the removal of the excess coating powder that is loose, combined with water or bulk goods.
Pinch Valves Perform Endless Cycles in Surface Treatment Applications
Thanks to the flexible modular system of AKO Pinch Valves, they come in a range of different configurations to suit these types of blasting and coating applications. In particular, the heart of the pinch valve which is the rubber sleeve has some fantatic qualities for these applications. The elastomer sleeve is available in abrasive free materials, and opens/closes in lightening fast times for super quick results. It is also the only wearable part of the pinch valve, and if used correctly, performs a pleasing amount of cycles with no problems.

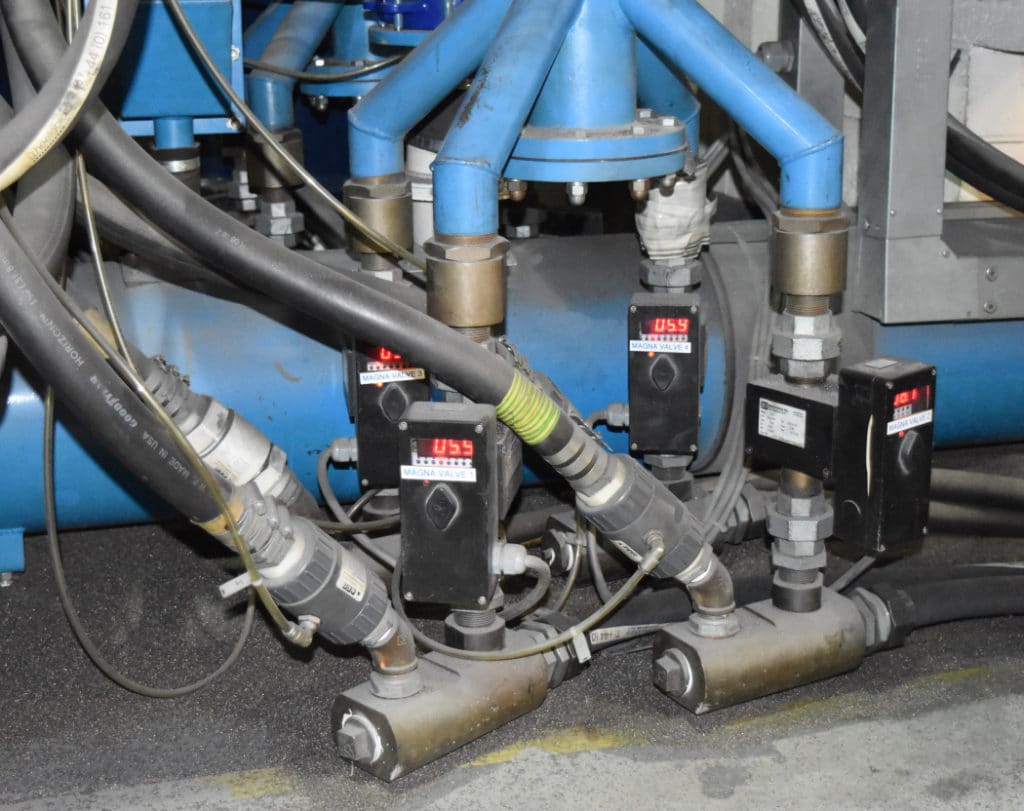
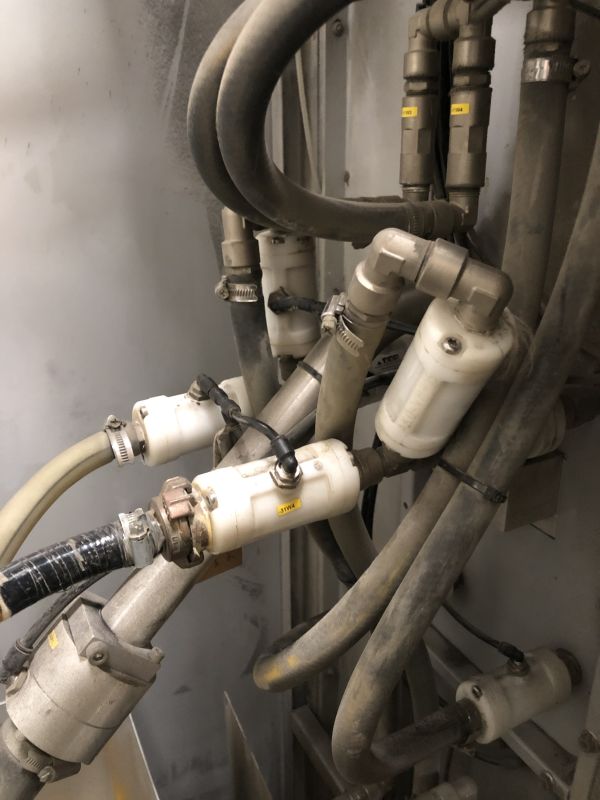