Pneumatic vacuum conveying is a method of pulling or sucking material through a pipeline. Many different types of material can be transported using vacuum conveyance, as well as vacuum suction pressure used for bag/container emptying or filling.
Usually, a vacuum pump is installed at the end of a conveying line in a separator vessel in which the suction air flows through a filter system to separate the transported goods. The goods are collected in this container and can be transported further or processed once the vacuum has been removed with the aid of valves. After the vacuum pump has been switched off, the pressure inside the pipelines and the separator vessel returns to the ambient pressure.
For the filter system to work at maximum performance, it needs to be regularly freed of any adhesions – so-called filter cakes. This is done by blowing a short blast of air against the filter. Once the adhesions have been blown away, the vacuum pump can continue its work.
In order to ensure that no constrictions or complete blockages occur at the valves in the vacuum pipe other than those desired, the valves in these sections must be suitable for vacuum operation.
There are many other positive characteristics with vacuum technology, as well as being used as a method for emptying containers. These include relieving the physical demands on employees and reducing damaging impacts on health such as from the formation of dust or the release of substances for example.
Pinch Valves and Vacuum Applications
Using pinch valves for vacuum conveying ensures both tightness and low wear with the addition of the AKO-Vac system. There is nothing to say that Pinch Valves cannot be involved with vacuum conveying with the use of the AKO-Vac accessory. The AKO-Vac system enables the Pinch Valve to be suited to the vacuum conveying sector.
To be able to use pinch valves in vacuum conveyance (from > -0.1 bar), they need to be fitted with a control unit that compensates for and thus counteracts the vacuum in the pipeline. This can also be achieved via a bypass that utilises the unpolluted process vacuum from the vacuum pump and guides it via the bleed vent on the solenoid valve to the inside of the pinch valve. If vacuum compensation using a control unit or bypass is not used, the installed sleeve will contract – due to the negative pressure – and will thus no longer ensure a constriction-free flow. In addition, the service life of the sleeve will be significantly reduced due to the increased strain placed on the inside of the sleeve.
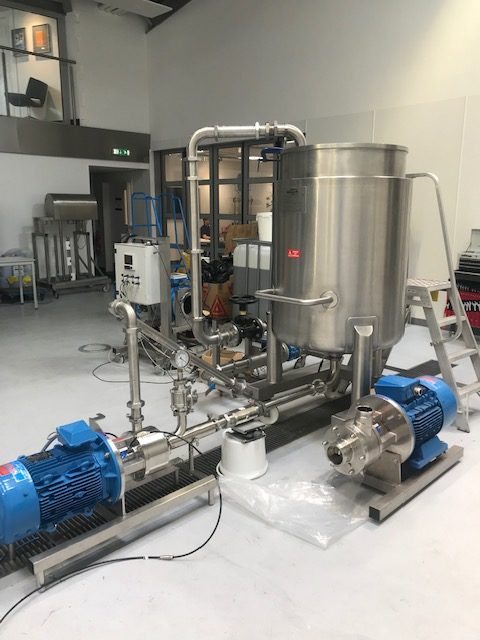
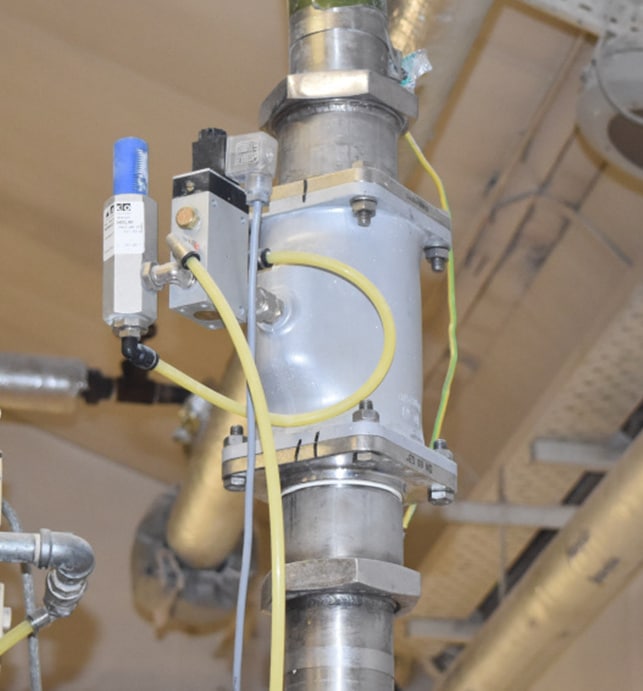
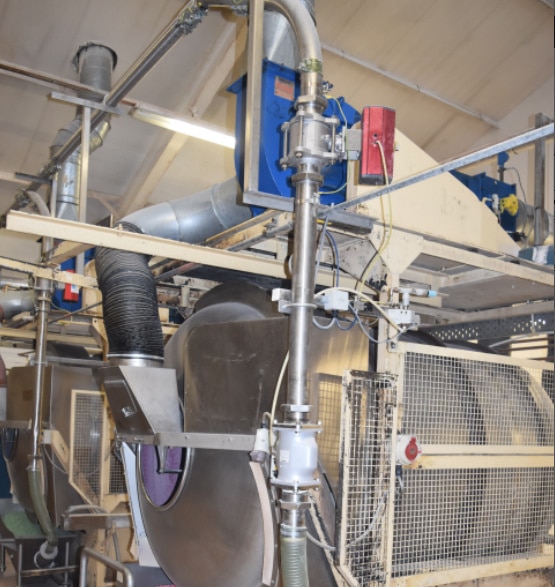
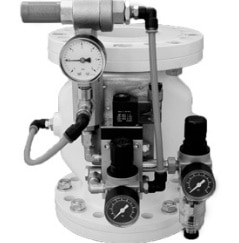
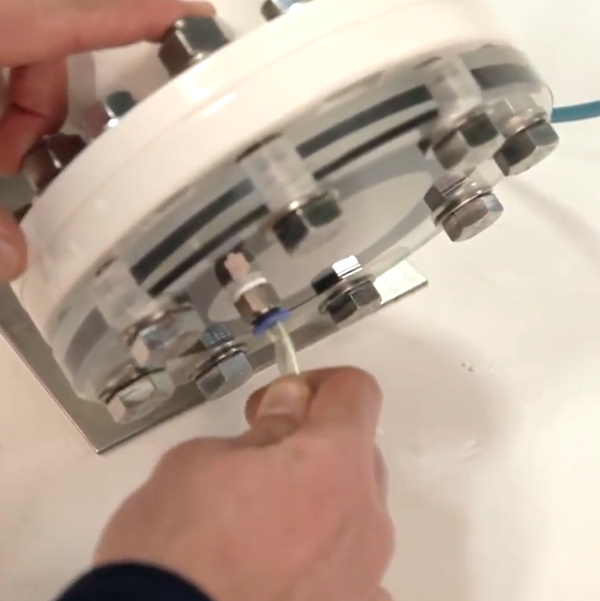
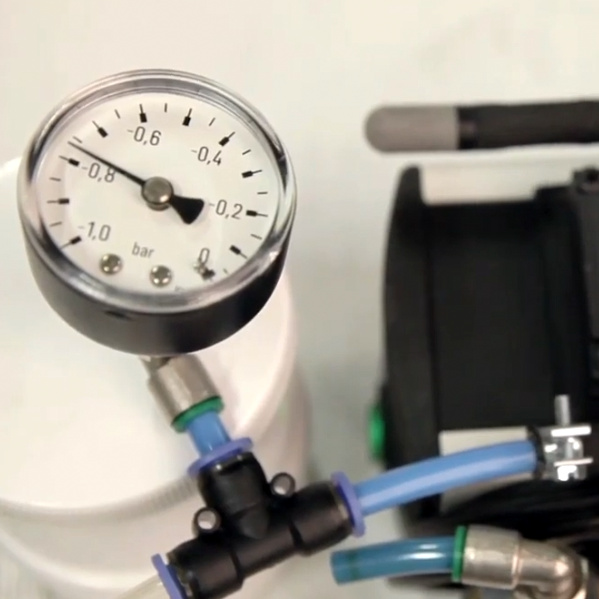
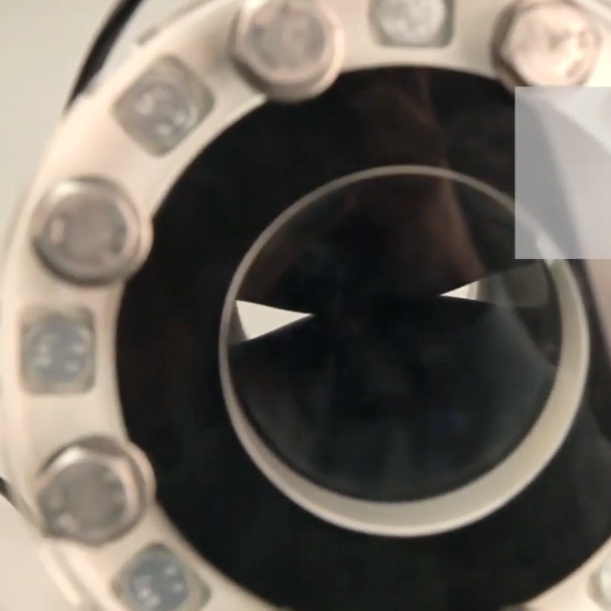
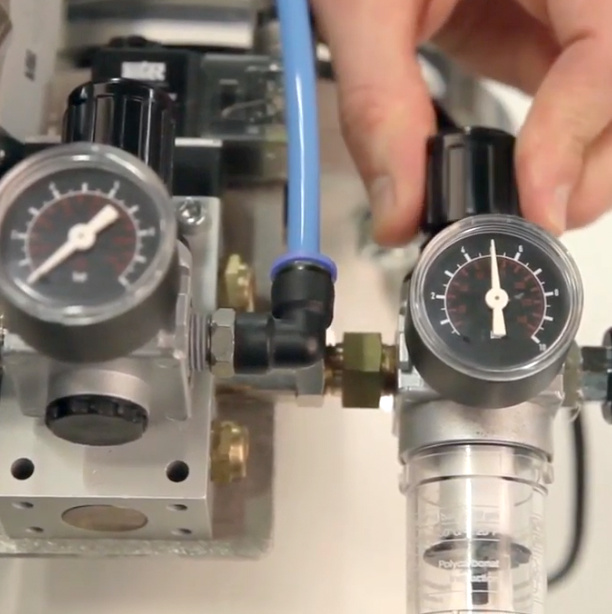
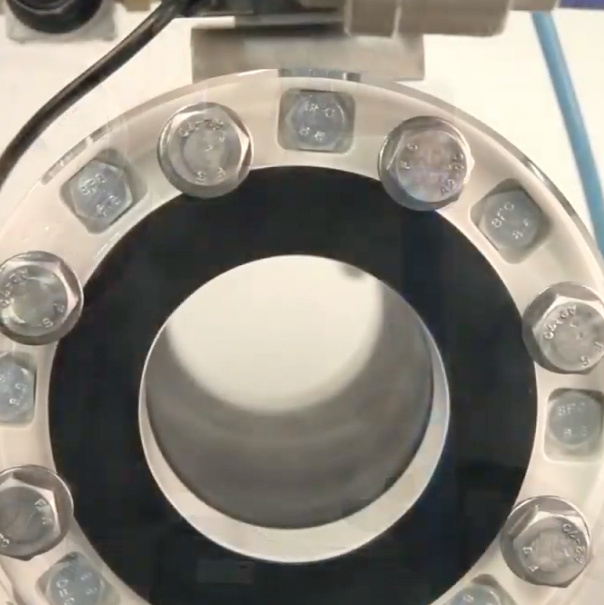
AKO-VAC Scenario
Vacuum is applied via a pipe inside the air operated Pinch Valve. The Pinch Valve Sleeve is almost fully closed with 0.8 bar vacuum inside it. With an AKO-Vac unit installed for vacuum generation, pressure is adjusted via a vacuum pressure setting, and with almost 6 bar pressure and a vacuum supply pressure of 0.8 bar, the Pinch Valve sleeve is once again fully open with the compensation of the AKO-Vac unit.
With the vacuum compensation then turned off, the Pinch Valve sleeve would then appear almost closed with 0.8 bar vacuum inside. Separate pressure settings of closing pressure should be availabe for the Pinch Valve. Only 1 – 1.5 bar closing pressure is required when an AKO Pinch Valve is used with vacuum.
AKO-VAC Basic & AKO-VAC Comfort
AKO offers two systems with the AKO-VAC Basic and AKO-VAC Comfort control units that equip the pinch valves ideally for use in vacuum conveyance. The control unit does not need to be fitted to the pinch valves directly but can be fitted so that it can control the negative pressure centrally and thus control multiple pinch valves at the same time.
View more information about the AKO-VAC units.