The pictures below show typical examples of Pinch Valve failures caused by the rubber sleeve either deforming, cracking, blistering or similar. There are usually simple reasons as to why this happens, and the solutions for how to prevent these pinch valve failures happening are straight forward to ensure the best possible lifetime of the sleeves.
Cracked, Torn or Ruptured Sleeves?
Damaged Pinch Valve Sleeve Examples
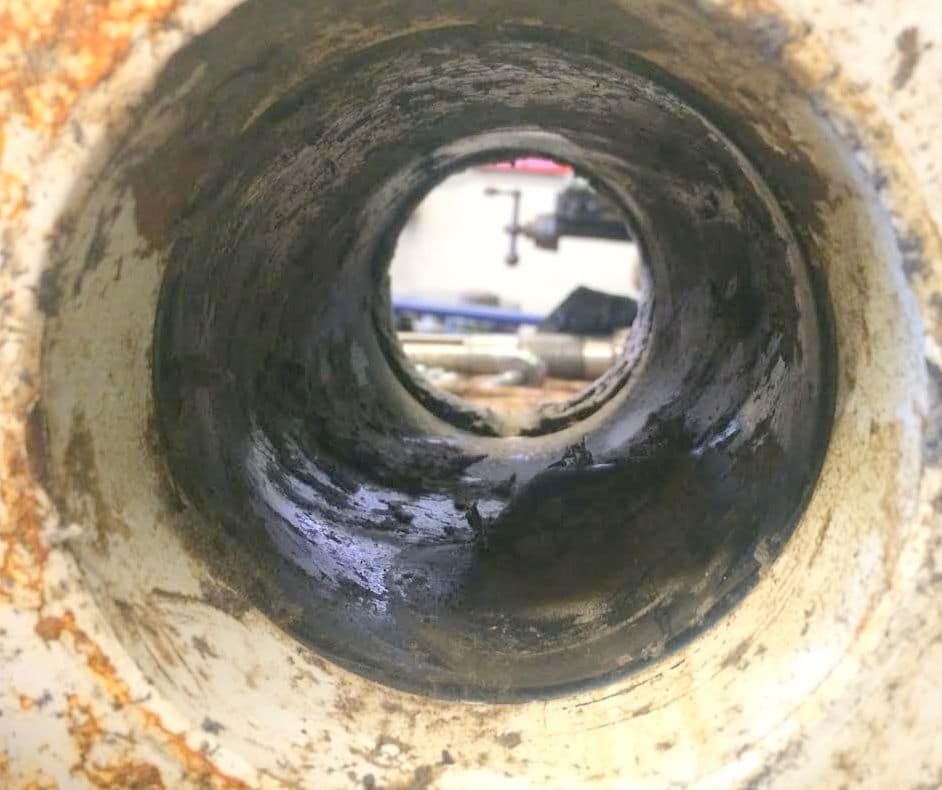
The incorrect rubber sleeve material has been used here. The application contains fatty oils so a Nitrile sleeve should have been used rather than Natural Rubber.
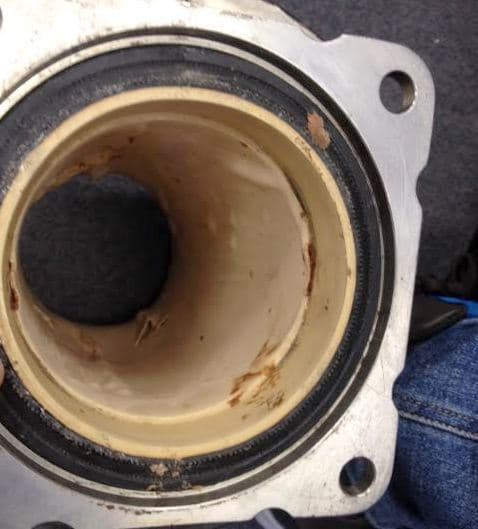
Blistered sleeve caused from Chocolate application – Temperature too hot.
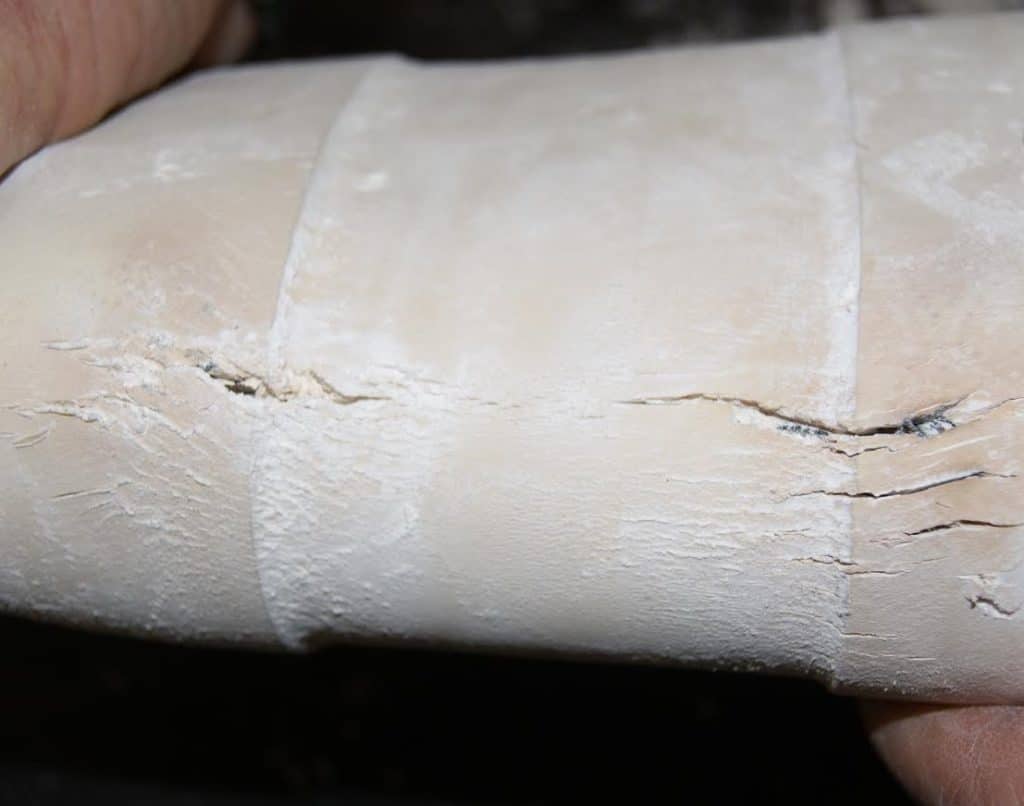
This rubber sleeve was used on a vacuum application where too much pressure has been used, causing the sleeve to tear from the outside.
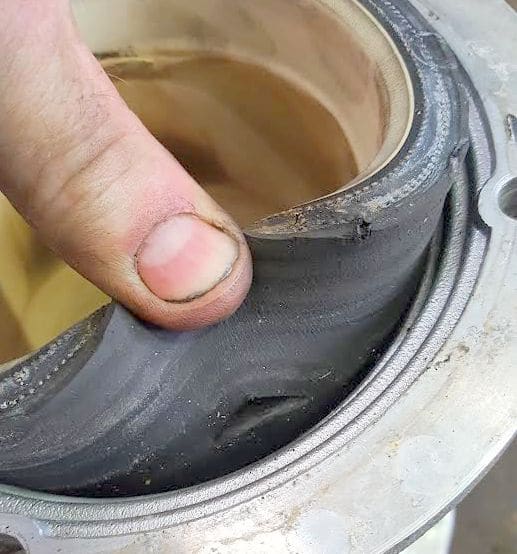
Re-sleeving mistake – See how to re-sleeve a Pinch Valve correctly.
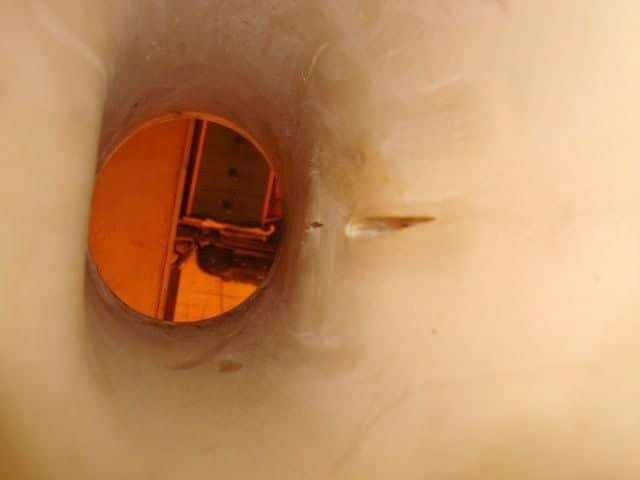
Split sleeve caused from a foreign body or sharp object inside the media flow.
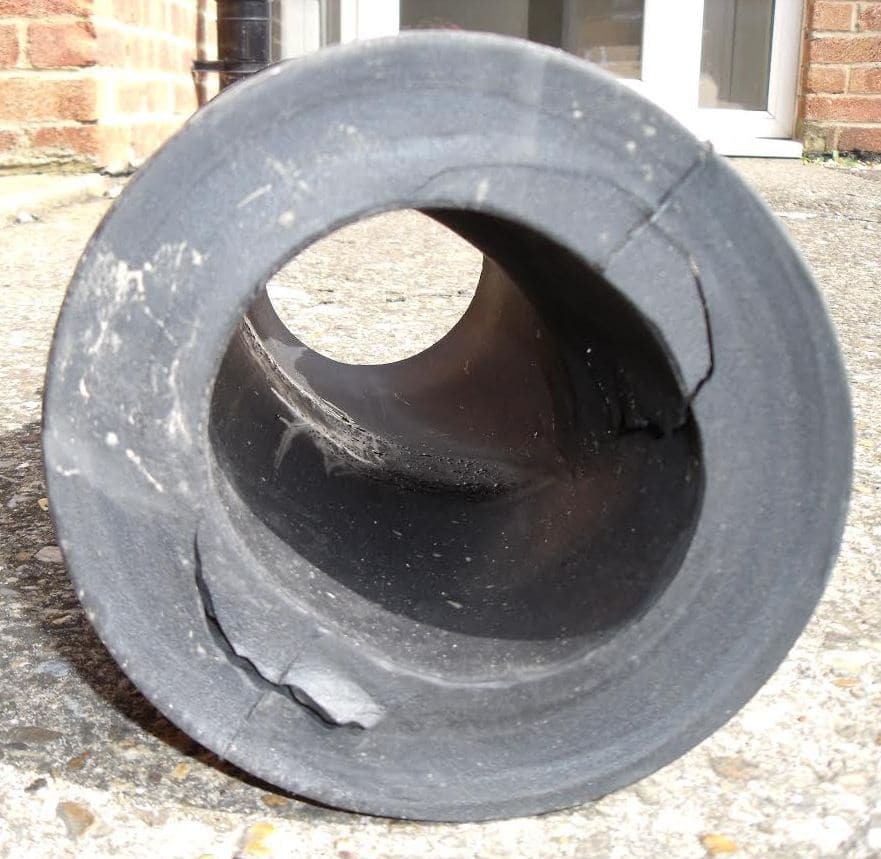
Incorrect installation of OV Normally Closed Pinch Valve in-line. The Pinch Valve should have been fully open when installing, but was in the closed position, causing the sleeve to crack when air was applied. See the installation instructions for correct installation.
Temperature Control
Is the temperature of the product passing through the Pinch Valve in your application within the temperature limits that the rubber sleeve can withstand?
–> For further information please see Pinch Valve Sleeve types & temperature ranges.
Pressure Control
Are you using the correct amount of line pressure for the product passing through the Pinch Valve?
–> AKO Pinch Valves have a limit to the amount of line pressure they can handle. Depending on the type of valve, this line pressure can vary. Please check the data sheet for the correct Pinch Valve in our Documentation area.
Are you using the correct control pressure for the amount of air to close the pinch valve?
–> AKO Pinch Valves require 2.5 BAR above the line pressure for the sleeve to close fully. For example, if the application is a gravity fed line with no air pressure pushing the product along, only 2.5 BAR is needed to shut off the Pinch Valve. In some cases, users may be shutting off the Pinch Valve using up to 4 BAR, 5 BAR, or even 8 BAR to close the Pinch Valve which is too high. This will shorten the lifetime of the rubber sleeve.
As another example: If the line pressure 3.5 BAR, then 5.5/6 BAR control pressure will be needed to close the Pinch Valve (2 BAR above the line pressure).
Re-Sleeving Pinch Valves
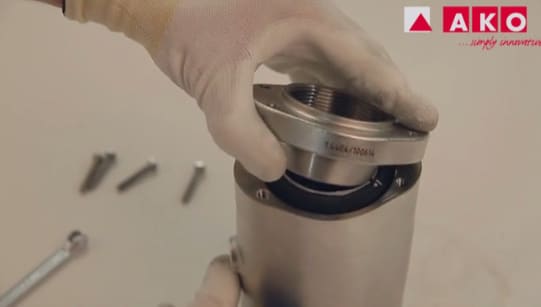
Have you carried out the correct assembly procedure?
–> Maintaining AKO Pinch Valves is quick and simple if carried out correctly. Replacing a rubber sleeve incorrectly can cause sleeve deformation.
The sleeve must be positioned with an equal length either side of the body. If the sleeve is protruding more from one side, when the Pinch Valve is pressurised this may pull the sleeve out, causing leaks or preventing the valve to close.
See our assembly videos for more information.
Sleeve Working Lifetime & Storage Life
The overall lifetime of a Pinch Valve Sleeve is not something we can say for sure. As each application is unique, it all depends on the different characteristics of the process. We do have some Pinch Valve case studies that might give more of an idea for some applications. This area is updated frequently so please check back.
We usually advise a 2 year shelf life for AKO spare sleeves. Therefore, if you know from experience that a sleeve needs replacing a lot sooner than 2 years in a particular application, it could be wise to keep spare sleeves on the shelf.
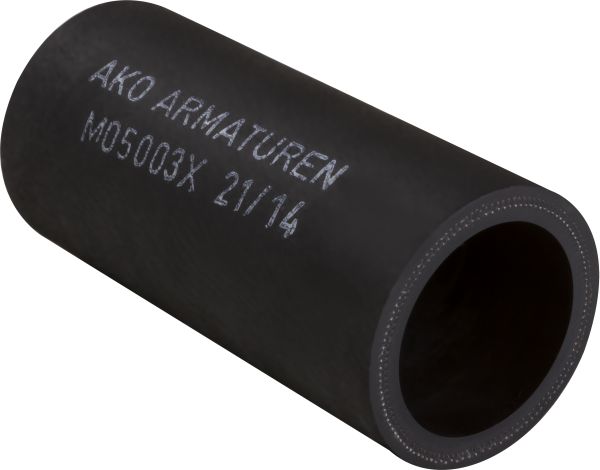